In the competitive plastics industry, a leading company faced a significant challenge: balancing the need for efficient, reliable production with a growing commitment to environmental sustainability. At the heart of their concerns were their extrusion systems, where any downtime could result in significant financial losses.
The company's search for a solution that could address these challenges while reducing emissions led them to RENK's SUPREX solution. SUPREX featured a highly efficient extruder gear unit, a product of RENK's optimized design and precision manufacturing. The system's design allowed part of the drive power to be supplied by a lower efficiency frequency converter, minimizing power losses and contributing to the company's goal of reducing its carbon footprint.
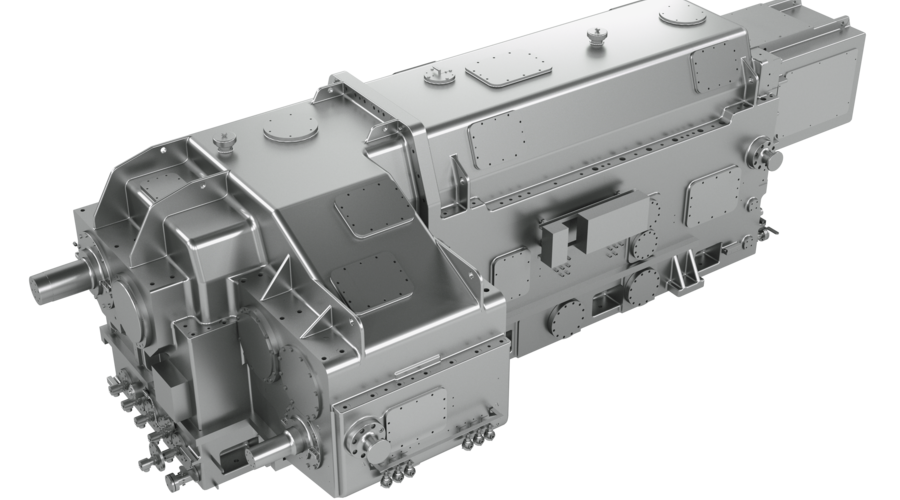
Recognizing the potential of SUPREX to meet both their productivity and environmental goals, the company invested in six extruder drives with additional options. "SUPREX fits perfectly to our commitment and strategy to reduce our carbon footprint. The system reflects a balance between economic viability and environmental responsibility. "
SUPREX fits perfectly to our commitment and strategy to reduce our carbon footprint. The system reflects a balance between economic viability and environmental responsibility.
Ready for the growth and demands of the plastic industry.
The future for the new extrusion business looks promising, and the challenges to reduce emissions are manifesting themselves in the industry. Jürgen Kuntner of RENK says: "Our latest developments for single and twin shaft extruder gears (SIREX and CAREX) and cost optimization programs (SUPREX Version B) offer a perfect match for the increasing demands of our customers.
The recent sales success reflects years of research and development, positioning RENK as a trusted partner to the industry.
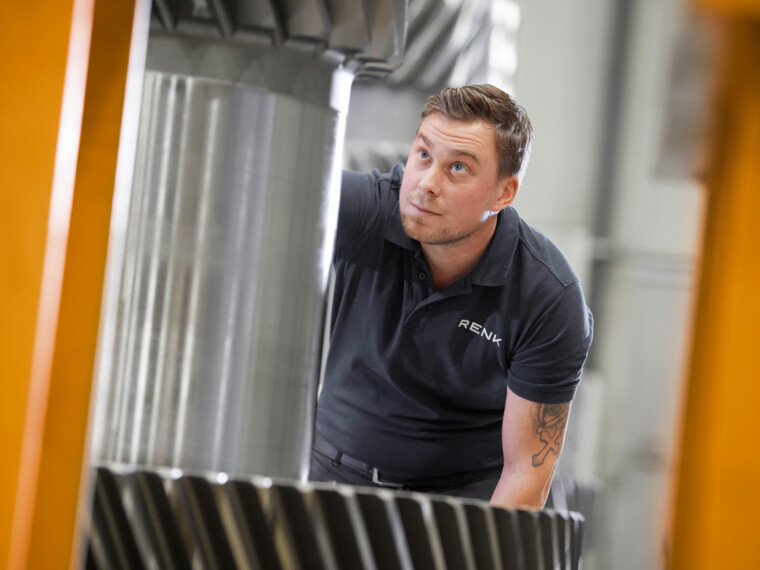
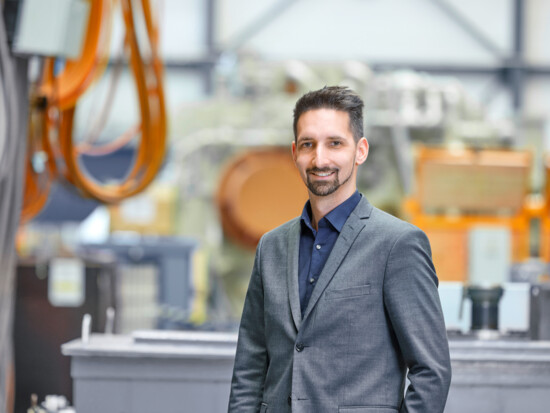
Get in touch with our engineering experts to discuss your questions and how we can contribute to your project success.