Doppelt so hoch wie der Kölner Dom und zwischen die Rotoren passt ein ganzes Fußballfeld: Moderne Windkraftanlagen sind Giganten der Technik. Solche Riesen erreichen inzwischen eine Leistung von mehr als 20 Megawatt und damit doppelt so viel wie noch vor zehn Jahren. Sie können den jährlichen Strombedarf von bis zu 15.000 Haushalten decken. Windkraftanlagen sind also Hoffnungsträger für die Energieversorgung von morgen und zugleich aber auch eine beachtliche Investition. Je nach Größe und Lage belaufen sich die die Kosten zwischen 2,5 und vier Millionen Euro je installiertem Megawatt Leistung. Entsprechend wollen die Investoren sicher sein, dass alle Systeme einwandfrei funktionieren. Das bedeutet, dass Getriebe, Generatoren und Rotoren umfangreiche Tests durchlaufen müssen, bevor sie beispielsweise in der Nordsee in Betrieb gehen.
Neue Technologien bedeuten auch, dass die Testanlage selbst ebenfalls neu entwickelt, konstruiert und erstellt werden muss. Bis dann die ersten Prüfungen erfolgen können, vergehen je nach Komplexität ein bis drei Jahre. Schon diese lange Zeit unterstreicht, wie eng und vertrauensvoll die Vernetzung zwischen Kunde und dem Systempartner RENK bei so einem Projekt ist. Der Prüfstand wird am Stammsitz in Augsburg vormontiert und auf seine Funktion getestet. Endgültig zusammengesetzt wird die Anlage erst vor Ort. Dann folgt eine Vielzahl von Tests und Optimierungen. „Jeder dieser Prüfstände ist ein einzigartiger Prototyp“, erläutert Schilp. Deshalb sei diese Form des Anlagenbaus so besonders und werde nur von sehr wenigen Unternehmen überhaupt angeboten.Die RENK Test System GmbH (RTS) gehört zu den wenigen Anbietern auf der Welt, die solche Prüfstände konzipieren und erstellen kann. „Wir kommen dann ins Spiel, wenn andere bereits an ihre Grenzen kommen“, erklärt Mathias Karrer, Geschäftsführer der RENK Test System GmbH. Die rund 150 Spezialisten aus Augsburg liefern keine Anlagen aus dem Katalog: Jeder Prüfstand ist ein Einzelstück, das speziell für den Kunden konzipiert ist. Die Teststände sind selbst zum Teil wahre Giganten, die eigene Gebäude mit 8 Meter tiefem Fundament benötigen und gerne 40 Meter lang sein können. So eine Testhalle wird von der Renk-Tochter ebenfalls geplant und der Bau dann anschließend betreut. „Wir bieten also Beratung, Entwicklung und den kompletten Anlagenbau aus einer Hand“, unterstreicht Karrer das schlüsselfertige Konzept von RTS.
„Wir sind schon bei den ersten Schritten dabei, weil wir so früh unsere Erfahrung einbringen können“, betont Andreas Schilp, der als Vertriebsleiter bei RTS mit seinem Team auch für die Projektierung der Prüfanlagen verantwortlich ist. „Wir gehen bei vielen Projekten an die Grenzbereiche der Technik“, erklärt Schilp. Geprüft wird zum einen, ob Getriebe und Lager einwandfrei funktionieren. Denn steht das Windrad einmal mitten in der Nordsee wären Reparaturen nur mit hohem Aufwand möglich. Geprüft wird aber auch, wie die die Anlage auf Schwankungen im Netz reagiert. Die sogenannte Grid Emulation kann verschiedene Fehlerfälle darstellen. Gleichzeitig dienen diese Tests auch zur Vorbereitung der Typzertifizierung für die Grid Codes verschiedener Länder. „Die RENK-Gruppe ermöglicht uns dabei eine hohe Wertschöpfungstiefe in technisch kritischen Teilen“, erklärt Karrer, wie die hauseigene Expertise in den Bau solch anspruchsvoller Prüfstände einfließt.
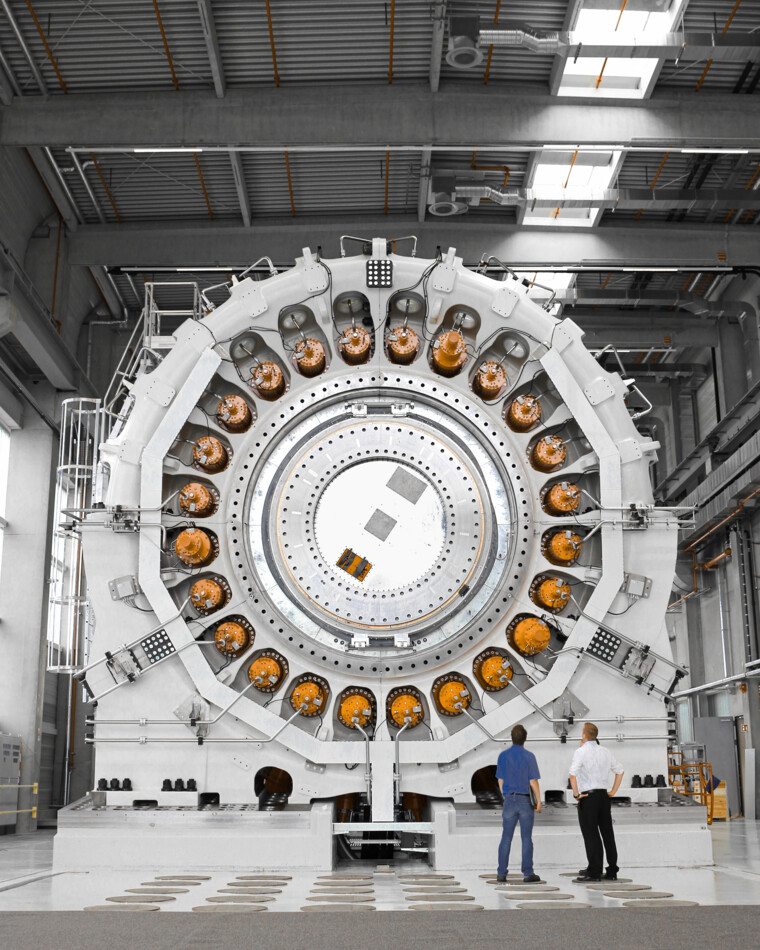
Im Fall der Windkraftanlagen testen die Ingenieure, ob beispielsweise Getriebe, Generator oder die Lagerungen den hohen Kräften gewachsen sind. Alles hat außergewöhnliche Dimensionen. So kann allein ein Wälzlager den Durchmesser von sechs Metern erreichen. Alles muss perfekt verarbeitet sein und miteinander harmonieren. „Die Qualität und die damit verbundenen Stärken bedeuten einen Mehrwert, den RTS seinen Kunden bietet. Den können diese dann wiederum an ihre Kunden weitergeben, was einen großen Wettbewerbsvorteil darstellt“, betont Karrer.
Die Qualität und die damit verbundenen Stärken bedeuten einen Mehrwert, den RTS seinen Kunden bietet. Den können diese dann wiederum an ihre Kunden weitergeben, was einen großen Wettbewerbsvorteil darstellt.
Komplexe Testanlagen wurden bei RENK zur Prüfung eigener Getriebe bereits in den 60er Jahren des letzten Jahrhunderts entwickelt und hergestellt. Der Automobilhersteller BMW war 1984 der erste externe Kunde. Schnell sprach sich herum, dass in Augsburg Spezialisten arbeiten, die anspruchsvolle Testverfahren beherrschen. So kamen mit der Zeit immer mehr Kunden aus unterschiedlichsten Industriebereichen dazu, die sich auf Prüftechnologie von RENK verlassen. Die gute Geschäftsentwicklung führte letztendlich zur Ausgliederung der Prüfstandentwicklung in die eigenständige RENK Test System GmbH, die nächstes Jahr bereits ihr 20-jähriges Firmenjubiläum feiert.
Gefragt sind die Prüfstände von RENK in der Luftfahrtindustrie. Hier werden beispielsweise die Getriebe von Helikopter auf Funktion und Belastung geprüft. Andere Kunden nehmen mit RTS-Anlagen ihre Turbinen unter die Lupe. Auch Bahnhersteller, -zulieferer und -betreiber greifen auf die Teststände aus Augsburg zurück. Der Einstieg in die Prüfung von Bremsen für Hochgeschwindigkeitszüge ist typisch für RTS. Der Bremsenhersteller Knorr-Bremse suchte einen Teststand für die Entwicklung der Bremsanlagen zukünftiger Hochgeschwindigkeitszüge, den es so noch nicht gab. Von RTS wurde erstmals so eine Prüfanlage realisiert, die mittlerweile zum Standard in der Entwicklung von Hochleistungsbremsen bei vielen Kunden weltweit geworden ist. Getestet werden bei Zügen aber nicht nur die Bremsen. Schlicht „The Machine“ nennen Eisenbahnspezialisten anerkennend den Teststand, der laufenden Betrieb auf einer Endlosschiene simulieren und dabei Radreifen und Achsen unter realer Belastung testen kann. Dabei erfahren die Experten viel über Verschleiß, Geräuschentwicklung und mögliche Belastungsgrenzen.
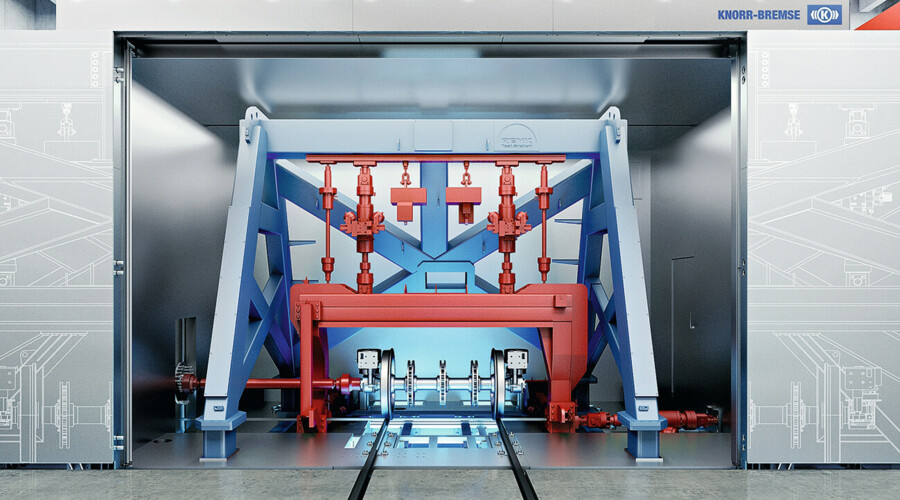
Die Prüfstände von RENK kommen nicht nur bei fertigen Produkten zum Einsatz. Sie sind oft die reale Nagelprobe für die Berechnungen und Idee aus den Entwicklungsabteilungen. Mit Hilfe zweier Prüfstände von RTS ergründet Mercedes-Benz im Werk Sindelfingen gerade, welche Geräusche die elektrisch angetriebene S-Klasse im Fahrbetrieb erzeugt und welche Quellen dafür verantwortlich sind. Die Entwickler großer Anlagen erfahren mit Hilfe von Prüfständen erstmals, ob ihre im Simulationsraum vorgedachte Konstruktion in der realen Umsetzung tatsächlich die gewünschten Ergebnisse liefert.
Bei der Entwicklung dieser ganz besonderen Anlagen steht bei RENK seit jeher der Nachhaltigkeitsgedanke im Fokus. Bei der Beschaffung eines Prüfstandes müssen kundenseitig neben der Funktionalität nicht nur die reinen Beschaffungskosten betrachtet werden. Prüfstände von RENK sind nicht selten 30 Jahre oder länger im Betrieb. Da spielen die gesamten Life-Cycle-Costs (LCC) eine große Rolle. Entscheidend ist hier die modular aufgebaute Software, die sich so an neue Testreihen und Bedingungen anpassen lässt. Das stellt sicher, dass der Kunde die Anlage auch für Produkte einsetzen kann, die erst in der Zukunft entwickelt werden. Die Prüfstände sich darum auf lange Betriebszeiten konzipiert, wobei viel Wert auf die Zuverlässigkeit gelegt wird. Der schonende Umgang mit Ressourcen oder größtmögliche Energierückgewinnung in Herstellung aber auch im Betrieb der Anlagen spielen dabei ebenfalls eine wichtige Rolle.
Ob Energie-Erzeugung, Mobilität oder Maschinenbau. Der Bedarf nach Testanlagen steigt weltweit rasant. „Somit ist unser Wachstumspfad als Trusted Partner für unsere Kunden in diesem Geschäftsfeld vorgezeichnet“, betont Karrer. Die Transformation in vielen Branchen erfordere neue Technologien und Verfahren, die entwickelt und dann getestet werden müssen. „RTS ist hier ganz vorn dabei. Das macht uns auch für ehrgeizige Techniker und Ingenieure interessant, die mit uns an einer nachhaltigen Welt mitarbeiten wollen.“
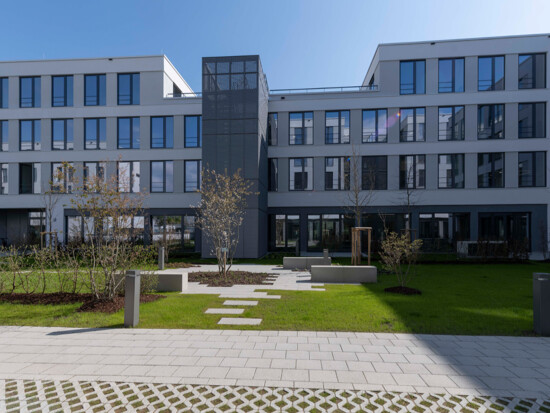
Setzen Sie sich mit unseren Experten in Verbindung, um Ihre Fragen und Anforderungen bezüglich spezieller Prüfstände zu besprechen.