The electrification of aviation has the potential to fundamentally change mobility and logistics in our society. With continuing population growth and vibrant megacities around the globe, Advanced Air Mobility (AAM) is an opportunity to connect people sustainably.
RENK Test System Test Systems Test systems assess technical components for function and durability. GmbH (RTS) has been supporting the development and qualification of conventional helicopter engines with its test rigs for decades and has similar experience in developing test rigs for hybrid and full-electric drivetrains. This knowledge and our experience are now proving crucial in the field of electric Vertical Take-Off and Landing aircraft (eVTOLs).
The RDDS test rig automation system makes the difference.
Before electric aircraft are allowed to operate in our cities, they must prove their absolute reliability and safety. And that is where RENK and our test rigs can be of high value. They can be used to simulate many operating situations and failure scenarios without the aircraft having to leave the ground in reality. Of great importance for these test runs is the latest version of the test rig automation system RDDS, the so-called RDDS.NG, developed by the experts at RTS. It is the first of its kind worldwide. It offers great flexibility and thus a wide range of test scenarios.
The operator can run the different test beds individually for component testing as well as all test beds simultaneously for testing the complete aircraft's electrical drive system. RDDS communicates with the aircraft's drive control units in real time. When the eVTOL takes off, all motors give the same upward thrust. However, if the aircraft needs to take a turn or other flight maneuvers become necessary, the motors have to give different amounts of thrust. For these situations, RENK's test stand offers optimal conditions and can set individual thrust requirements for each of the eight motors.
Besides this usual operation conditions, the validation of safety and redundancy features of the eVTOL is crucial for its certification. Therefore, a set of critical failures can be inducted by the test stand, for example power failures and shortcuts. The Test engineers can examine cause and effects with a powerful time-synchronized measurement system and back up the certification process with data.
In order to keep up with the fast development cycles in the AAM area, our test rig allows for quick adaption to new testing requirements by simulating missing elements with Hardware in the Loop (HIL) and Software in the Loop (SIL) functions.
Hardware in the Loop (HIL) and Software in the Loop (SIL)
In order to keep up with the fast development cycles in the AAM area, our test rig allows for quick adaption to new testing requirements by simulating missing elements with Hardware in the Loop (HIL) and Software in the Loop (SIL) functions. These simulations can replace physical parts or software functions of the test article, as well as environmental conditions.
Many experts believe that Advanced Air Mobility will most importantly bring more sustainability into logistics. The tasks involved in creating and using this unique test stand have therefore proven to be entirely in line with RENK's philosophy of emission-free and sustainable propulsion solutions.
We are very proud to support the development and certification of electric aircraft engines – as a Trusted Partner for the industry.
The coolest facts in a nutshell
RENK has a very large experience from the successful design, manufacture and operation of test rigs for more than 60 years.
It is the first test rig of its kind. The heart of the test stand, the RDDS automation system, is customized to meet specific customer requirements, but its basic structure has been successfully tested in hundreds of test stands.
With this test stand, up to eight rotors can be controlled simultaneously, but completely independently of each other, in order to test a wide variety of flight situations such as landing, take-off and attitude.
By inducing customer-specified mechanical and electrical faults, safety features can be reliably validated.
Simulation of components (e.g. batteries) or environmental conditions (e.g. wind) in the test rig automation system RDDS is possible with Matlab/Simulink® integration.
By means of predefined automatic programs we enable a complete reproducibility of test runs and thus a complete redundancy of test tasks and comparability of test results.
An entire team of experts at RTS is dedicated to the continuous development of RDDS capabilities. Future test rigs, for example, will be able to represent each rotor blade as an individual part when simulating the rotor forces on the motor shaft.
RENK offers worldwide service – via remote maintenance or personally on site, provided by the experts at our locations around the globe.
Do you need more information about our test rig solutions for the aviation industry?
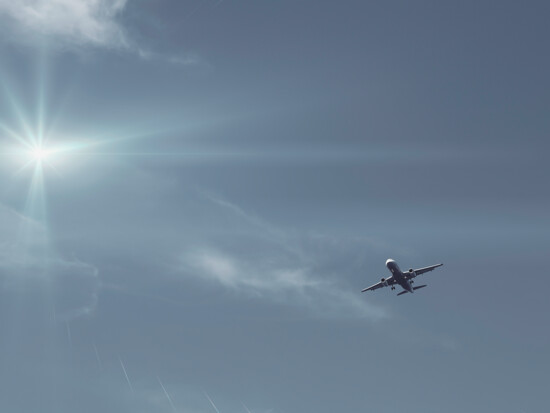