RECOVAR®-E: Next-generation variable-speed drive
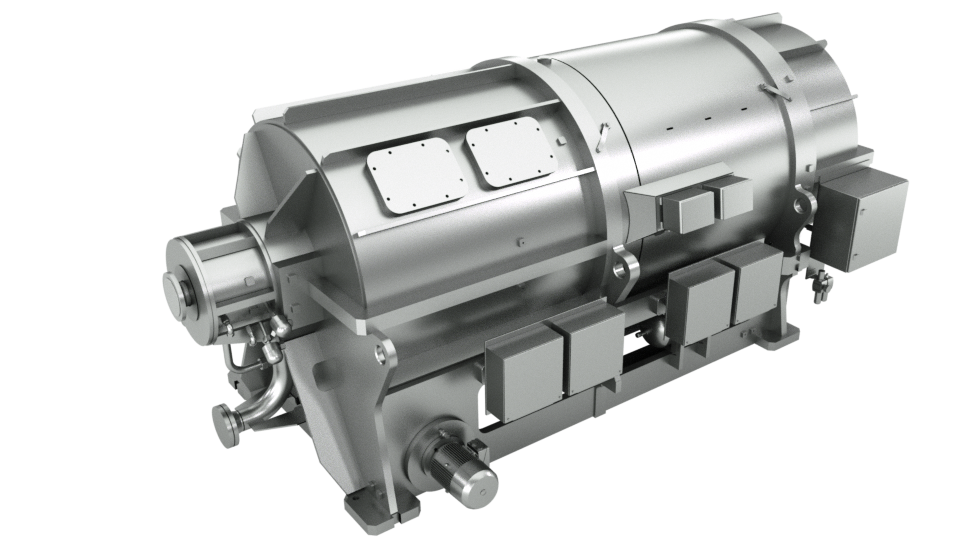
RECOVAR®-E stands for RENK ECOnomic VARiator and is RENK’s variable-speed gearbox, which impresses with exceptional reliability, maximum efficiency at all operating points, and energy recovery under partial load.
Application areas for RECOVAR®-E include variable-speed pump and compressor applications in the oil and gas industry, petrochemicals, chemicals, hydrogen production, and other process industries. The RECOVAR®-E offers high flexibility with gear ratios from 3 to 15, a variable speed range from 70 to 105% at constant input speed, power transmission Transmission A vehicle transmission transfers engine power to the wheels and allows for variable driving speeds. up to 150 MW and an efficiency of approx. 97%.
The system combines proven mechanical technology with state-of-the-art, industry-grade SI drives and electronics. Thanks to the extensive experience of our engineers and production capabilities, RECOVAR®-E offers customers the best of both worlds:
- Maximum availability, thanks to the back-up functionality of the fixed-ratio mode
- Highest efficiency through the use of slide bearings Slide Bearings Slide bearings enable low-friction movement between fixed parts. and a power-split mechanism, leading to increased profits and reduced emissions
- Intelligent, simple design to ease on-site installation and maintenance
- Small footprint, making it the preferred choice for offshore applications
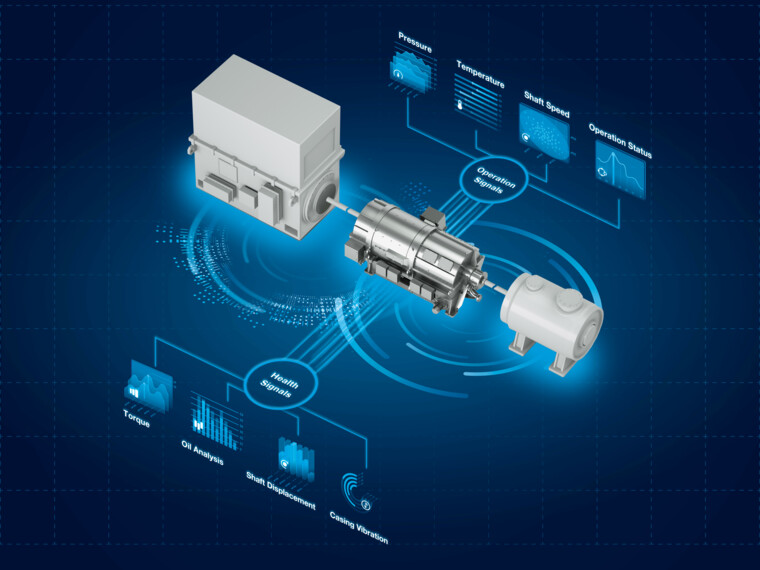
Why RECOVAR®-E is THE solution for a variable drivetrain system
RECOVAR®-E is designed not only for variable-speed operation but also for continuous fixed-speed operation. This ensures maximum system availability, as it can continue to operate at a fixed speed if the superimposing motor is disengaged via the safety brake. In this mode, RECOVAR®-E functions like a planetary gearbox Planetary Gearbox A planetary gearbox is a compact unit with high torque transmission and efficiency. without an annulus, reducing system downtime.
Induction motors are known for their ruggedness in harsh environments. Their simplicity is a key factor for maintenance, service, and safety. The SI motor is an induction motor with water- or oil-jacket cooling. In the event of a power failure, a disc brake safely stops the SI drive.
RECOVAR®-E includes temperature monitoring of the planetary bearings using wirelessly transmitted RFID (Radio Frequency Identification). Slide bearings on all shafts are essential for continuous operation.
Utilizing a concept inspired by parallel shaft gear units, this system improves the accessibility and serviceability of planetary gear systems. The direct-drive SI design significantly reduces component count, lowers the risk of mechanical failure, and simplifies maintenance procedures.
To maximize lifespan, all rotating components use slide bearings Slide Bearings Slide bearings enable low-friction movement between fixed parts. , eliminating rolling-element wear and removing the need for a planned Mean Time Between Overhaul (MTBO). The optimized system architecture also reduces the Total Harmonic Distortion (THD), lessens electrical stress, and improves overall drivetrain efficiency.
For applications requiring uncompromised operational safety, an optional redundant inverter for the SI motor ensures continuous performance and enhances system stability and availability.
The RECOVAR®-E system is designed for efficient inspection and disassembly without removal from the shaft train. The mechanically simple design without a ring gear allows for easy access and serviceability compared to conventional planetary gearheads.
The planetary shafts and their bearings are easily accessible and can be disassembled without complicated intervention. In addition, the input and output shafts can be serviced independently without affecting the alignment of the housing. This design reduces crane capacity requirements along the shaft axis, optimizes maintenance, and minimizes downtime—enhancing both reliability and long-term operational efficiency.
The simple technical gearbox solution of the RECOVAR®-E achieves the lowest inertia among known compressor drive solutions with variable ratios. This reduces startup torque demand and mechanical stress on the drivetrain. The SI motor ensures a controlled speed ramp-up, which relieves the main motor, optimizes power distribution, and reduces the need for oversized motors.
Electrically, RECOVAR®-E achieves minimal harmonic distortion (THD)—well below IEC acceptance thresholds. As the SI drive requires only limited power for speed control, the inverter size is significantly reduced compared to full VFD solutions. This leads to lower electrical system load, greater grid stability, and higher overall efficiency.
RECOVAR®-E is a cost-effective solution when a high-speed drive system over 3 MW requires variable-speed control, which applies to around 50% of all compressor and pump systems.
The SI principle in the RECOVAR®-E’s differential gearbox is used to control the output speed above and below the gear ratio of the speed increaser. Unlike conventional SI setups, our SI motor is directly coupled to the planet carrier. The entire system uses RENK’s proven slide bearing Slide Bearings Slide bearings enable low-friction movement between fixed parts. technology for maximum efficiency and availability.
Where space and weight are limited, RECOVAR®-E is the answer. The inverter requires less than 20% of the power compared to full-size VFDs, resulting in minimal thermal load on control cabinets and compact inverter dimensions.
The superimposition system (SI) uses an induction motor controlled by an active front-end inverter (VFD) to drive the planet carrier. This allows precise speed control and efficient power distribution within the drivetrain.
When the SI motor is inactive, the output speed is determined solely by the input speed and gear ratio. Running the SI motor in generator mode reduces the output speed and recovers electrical energy. Conversely, in motor mode, the SI motor increases output speed as needed.
The SI motor is tailored to torque and speed demands, ensuring the ideal balance between performance and efficiency. Its low energy consumption and high efficiency—along with the VFD—significantly boost overall system efficiency, outperforming traditional variable-speed solutions.
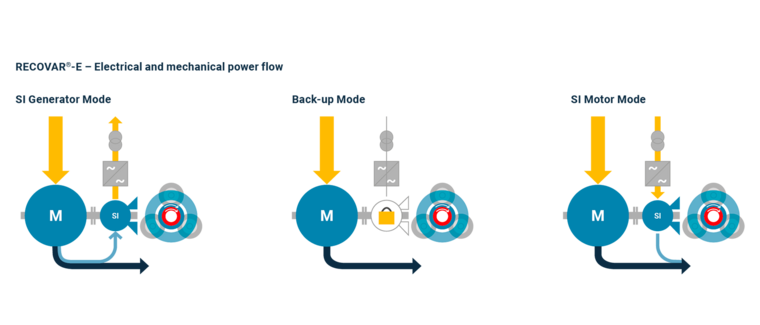
RECOVAR®-E supports a wide range of input speeds and offers output speeds from 4,000 to 20,000 rpm, enabling smooth integration into various industrial applications.
Typical speed control range is 70% to 105%, with tighter ranges offering even higher efficiency and lower operating costs. Larger control ranges are also possible depending on application. Efficiency figures refer to the main motor, as total drive power is split between main and SI motors.
For turnkey drive projects, RENK can provide detailed specifications and offers for the main motor to ensure optimal system configuration.
Discover how RECOVAR®-E revolutionizes variable speed drives with innovative superimposition technology. Experience unmatched efficiency, reduced maintenance, and maximum operational reliability. Watch the technology in action and see why RECOVAR®-E is the future of drivetrain solutions!
RECOVAR®-E is engineered for maximum availability and cost-efficiency. With a Mean Time Between Critical Failures (MTBCF) of over 30 years, it minimizes unplanned downtime and lowers maintenance costs.
The direct drive SI concept provides a technically simple solution with a low number of components. The use of hydrodynamic plain bearings only results in a significantly longer service life compared to designs with wear-prone roller bearings. Even in the event of an SI motor power outage, the system continues operation at fixed speed, ensuring process continuity.
An optional redundant inverter further enhances reliability. The integrated real-time condition monitoring (RVM) enables predictive maintenance, helping avoid costly repairs and production halts. By reducing lifecycle costs and increasing uptime, RECOVAR®-E is a smart investment in efficiency and reliability.
RECOVAR®-E delivers best-in-class efficiency, achieving a total system efficiency (including main motor) of about 97%. Through an optimized mechanical-electric hybrid overlay gearbox, unnecessary energy losses are minimized.
Compared to traditional solutions, this leads to significant energy savings—a 5% improvement over a full inverter solution in a 10 MW application can save at least €200,000 annually in energy costs.
Its low THD makes it ideal for decentralized power grids, and the optimized power distribution allows the use of smaller (typically 690V) and more efficient inverters, reducing operating costs. RECOVAR®-E means lower energy consumption, reduced costs, and a future-ready, sustainable drive solution.
This system is designed for seamless integration into a wide variety of applications and offers variable-speed control for compressors and pumps from 4,000 to 20,000 rpm. Unlike conventional drives, it allows precise speed adjustments with minimal energy loss, ensuring optimal performance under all conditions.
The compact design and low inertia of RECOVAR®-E simplify integration into both new and existing systems. Its modular architecture allows customization to specific power and speed needs, reducing the need for costly modifications. Whether for energy savings, load matching, or future expansion, RECOVAR®-E offers flexibility without compromise.
With a much smaller footprint than conventional variable-speed solutions, this system is ideal where space and weight limitations are critical. Its efficient power distribution and compact inverter reduce the need for oversized components and minimize required installation space in electrical rooms.
The reduced heat load also means less cooling is needed, further boosting system efficiency. By eliminating bulky transformers and oversized inverters, RECOVAR®-E integrates easily into existing infrastructure—reducing installation costs and improving space utilization, without compromising performance or efficiency.
The system is designed for easy access and minimal maintenance effort, enabling on-site inspection and disassembly without removal from the shaft line. The mechanically simple gear solution allows direct access to planetary shafts, making planets and bearings easy to replace.
Additionally, input and output pinions can be serviced independently without disturbing gearbox alignment—cutting maintenance time and lifting capacity requirements.
To further enhance efficiency, the system features real-time condition monitoring via RENK’s Vibration Monitor (RVM), continuously collecting data on vibrations, temperatures, and operating conditions. This enables predictive maintenance, reducing unplanned downtime and extending service intervals.
With fewer components and no scheduled MTBO (Mean Time Between Overhaul), RECOVAR®-E ensures lower lifecycle costs and maximum availability.
Technical Data
Power: | 3–150 MW |
Low speed shaft: | < 1 800 rpm |
High speed shaft: | 4 000–25 000 rpm |
Compressor speed range: | 70–105% |
Transmission Transmission A vehicle transmission transfers engine power to the wheels and allows for variable driving speeds. ratio: | 3–15 |
Toothing: | Straight and double helical |
Efficiency: | 97% |
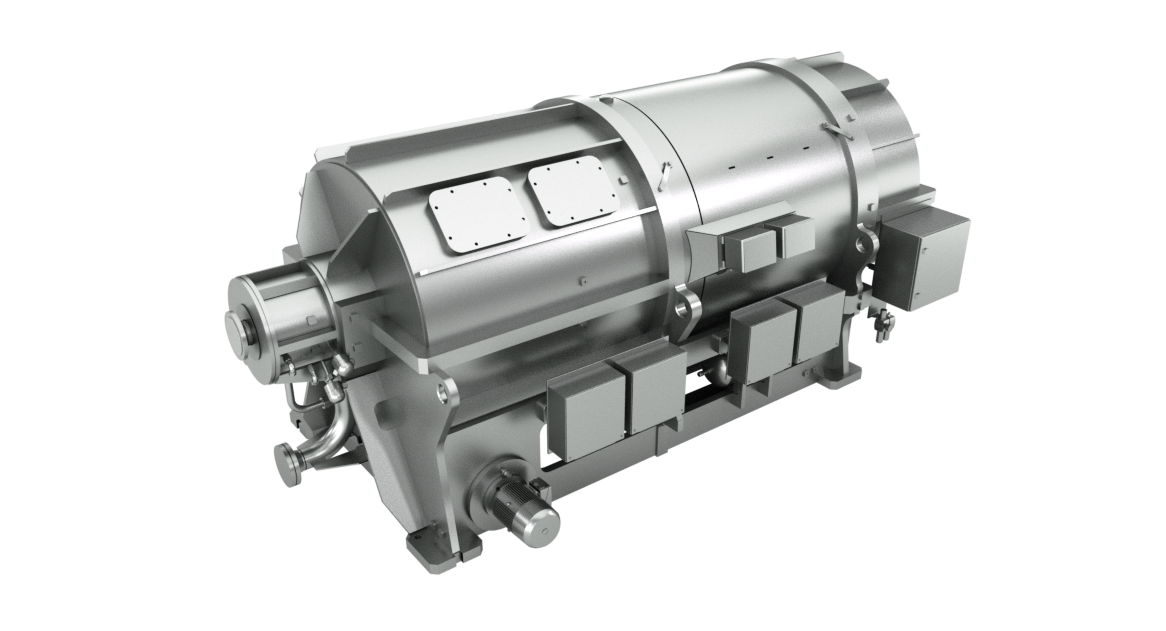
Downloads
- RENK RECOVAR-E (3.4 MB)
E-Mail angeben
Bitte geben Sie Ihre E-Mail-Adresse an, um den Download zu starten.
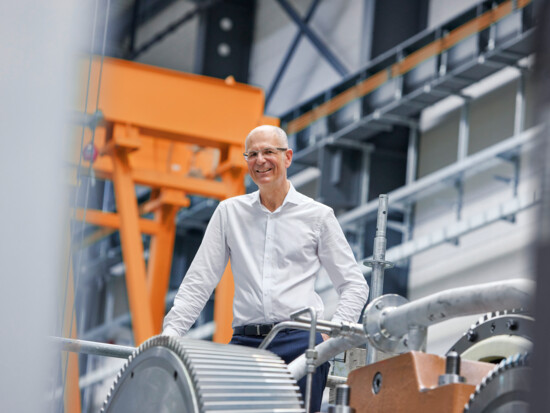
Get in touch with our experts in case of any questions.