Pitch bearing test rig
- 01Simulation of real installation situation
- 02Detailed measurement of bearing efficiency
- 03Load compensation
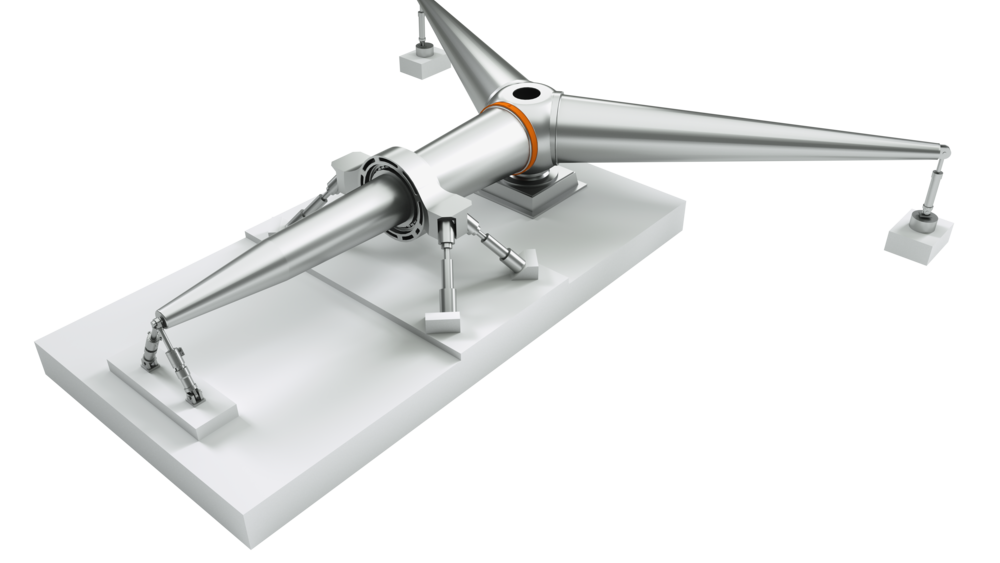
Our technologies for your demands
As the rotor blades of multi-megawatt turbines become longer and longer, the load on the pitch bearings also increases more and more. Testing these bearings under real installation conditions and reproducible test runs is therefore becoming increasingly important.
In addition to a simple linear load on the pitch bearing, the customer can choose from the following additional options:
- Controlled rotation of the blade
- Integration and control of the real pitch drive
- Integration of the real pitch control and communication with the test stand control system in real time to reproduce real dynamic load conditions.
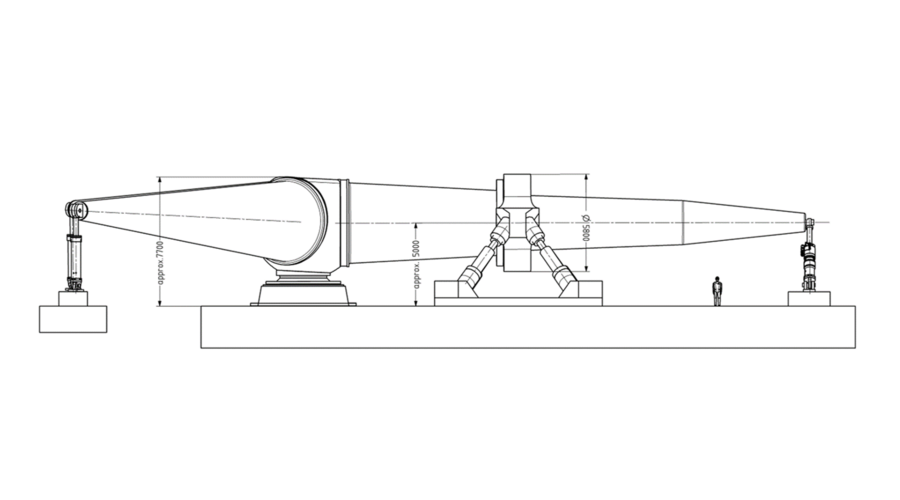
Use of the real hub
The load on a wind turbine pitch bearing is determined quite significantly by the design of its surrounding interface assemblies. For this reason, RTS recommends using the original hub as the test fixture and simulating the blade geometry for load application. Finally, to achieve a real hub deformation, this hub is also be fixed at the other two pitch bearing locations.
Spot-on individual measurements
Disturbing influences of the test rig such as vibrations or friction losses can strongly influence the measurement on the bearing to be tested. Due to the consistent use of frictionless actuators and plain bearings, sophisticated designs and state-of-the-art manufacturing processes, we can offer our customers optimum test conditions with RENK test rigs. In this way, even many simultaneously recorded measured values can be optimally separated from each other and therefore test item values can be precisely analyzed without interfering effects.
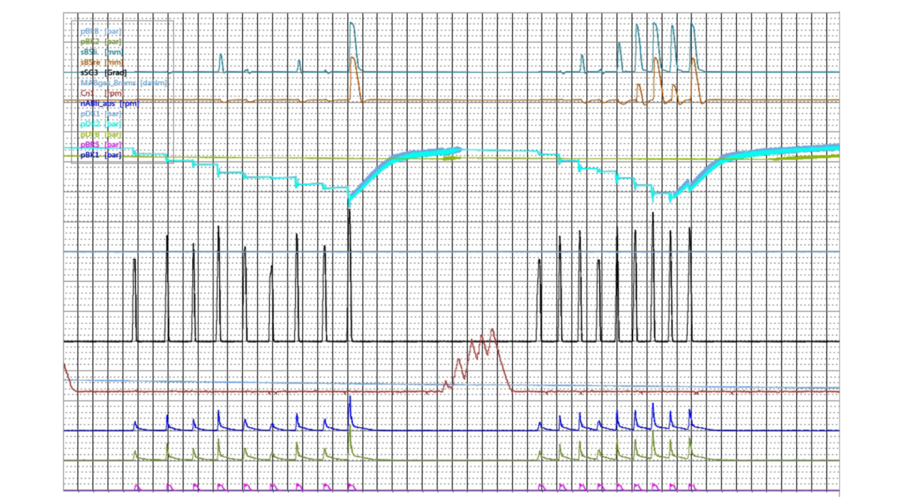
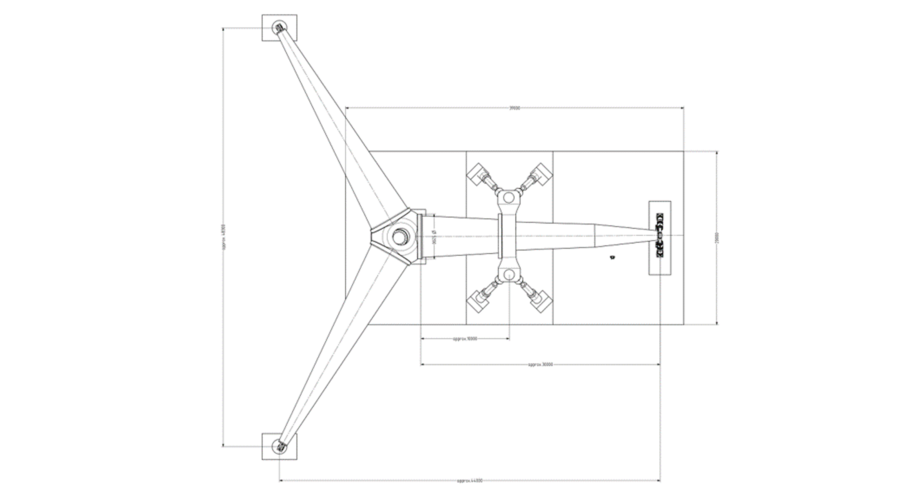
Simplifying the foundation
Fixing the hub at all three pitch bearings leads to a uniform distribution of the tensile forces in the foundation. The central main foundation of the hub can thus be built much more easily and cost-effectively. Additional load reaction blocks, which are necessary when testing a single rotor blade or pitch bearing, are not needed with this arrangement.
Features
- Pitch bearing test with original hub and uniform load distribution
- Low-friction and low-vibration test rig design
- Unique measurement and control accuracies
- RENK RDDS test bench automation and data acquisition
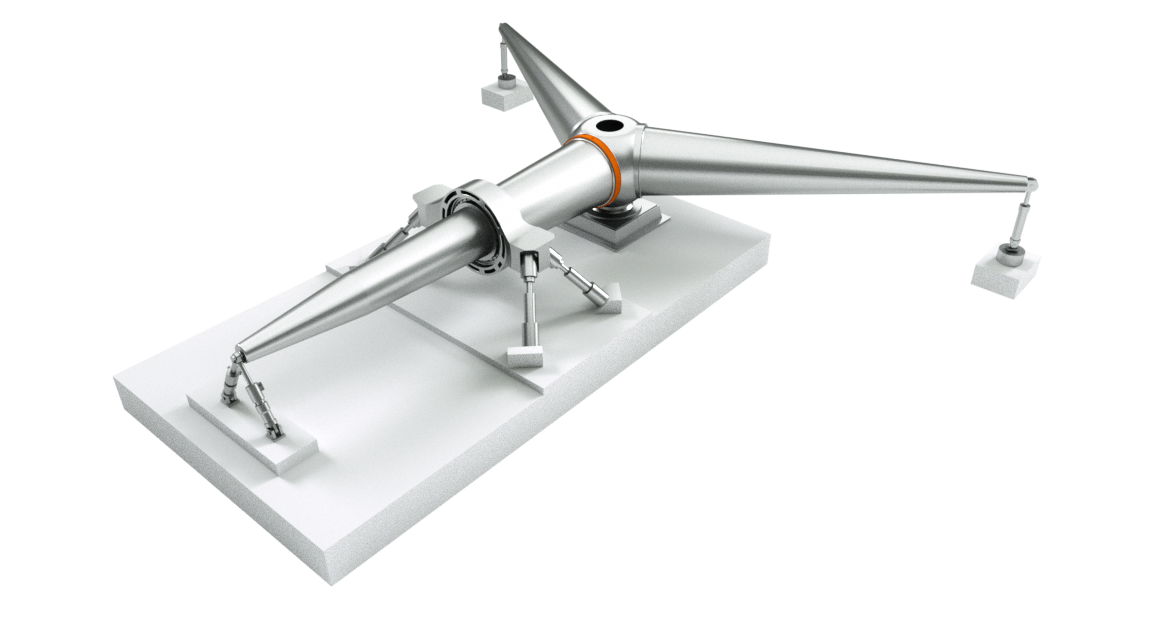
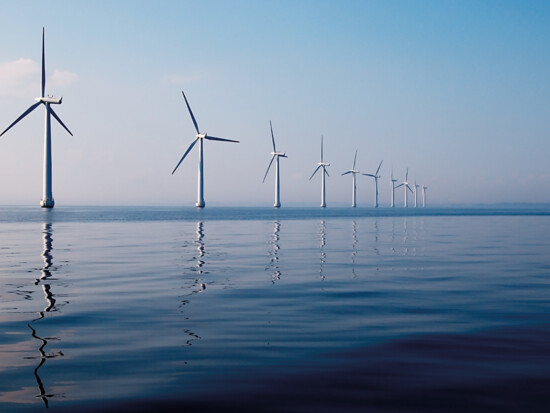
Get in contact with our experts from
Team Windpower: