Modernisation of an aged brake test rig at the Kolejnictwa Railway Institute
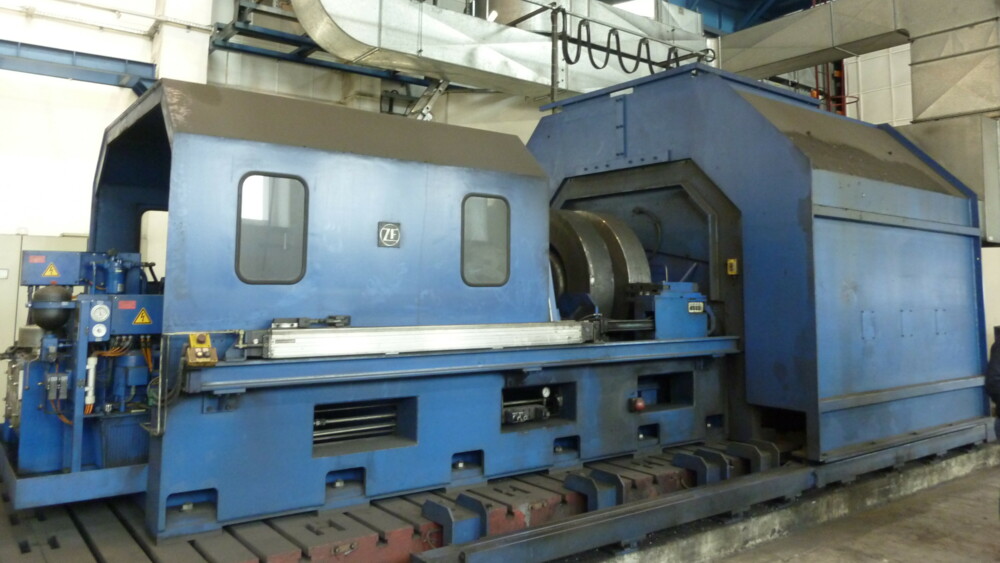
Trusted Partner
As a Trusted Partner for sustainable test rig solutions, we not only install new systems for our customers, but also take care of all the service activities required for the smooth operation of a test rig. We also take on the servicing of systems not supplied by RENK, including a wide range of modernisation measures. Because a sensible extension of the service life of existing systems is climate-friendly and cost-saving.
The Instytut Kolejnictwa is the most renowned Polish research organisation operating in the field of rail transport. The research institute, which has been operating for 70 years, has its own research track and numerous facilities required for research and scientific work in the field of rail transport. The Instytut Kolejnictwa is also recognised by the Polish Centre for Accreditation as a product certification body and a calibration body. To test the friction properties of brake components, the Rolling Stock Testing Laboratory attached to the institute has an aged flywheel brake dynamometer, which was modernised by RENK Test System Test Systems Test systems assess technical components for function and durability. GmbH (RTS) and adapted to today's testing standards.
In order to guarantee the future viability of its range of tasks, the Instytut Kolejnictwa decided in favour of a complete electrical/digital modernisation of the test rig built in 1997. While the mechanical components of such test rigs are often still in an acceptable condition decades later with appropriate maintenance, the electrical and electronic assemblies are no longer up to today's standards and pose a high risk to the reliable operation of the test rig due to a lack of spare parts.
The complete modernisation of the flywheel brake dynamometer was carried out by RENK on a turnkey basis.
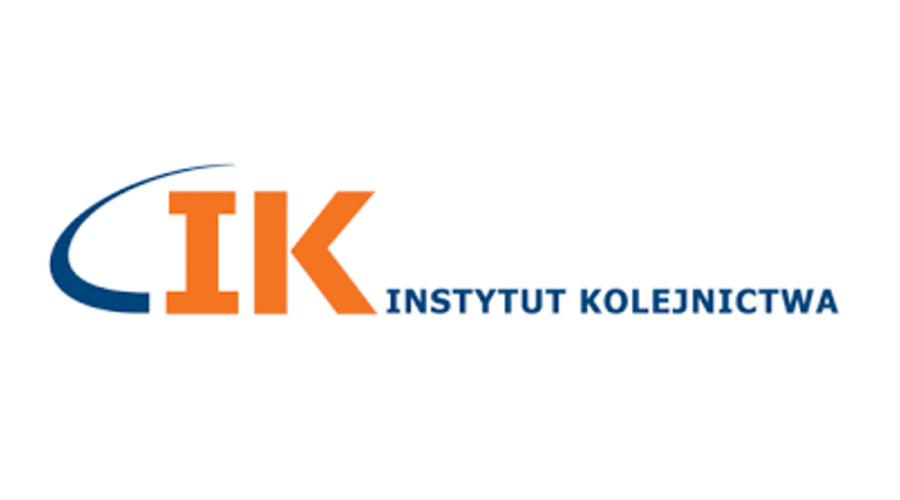
Digital modernisation
In order to be able to reliably perform future testing tasks in the familiar environment, the Rolling Stock Testing Laboratory decided to carry out the following modernisation work on the existing flywheel mass brake dynamometer:
- Construction and installation of a new control and monitoring system
- Construction and installation of a new system for recording and processing measurement data from the tests
- Construction and installation of a new system for programming the test rig ( designing test programmes)
- Construction and installation of a new system for monitoring and diagnosing the test rig and components
- Construction and installation of a new wet test device
The modernised test bench must meet all the requirements of UIC certification for testing friction pairings of train brakes.
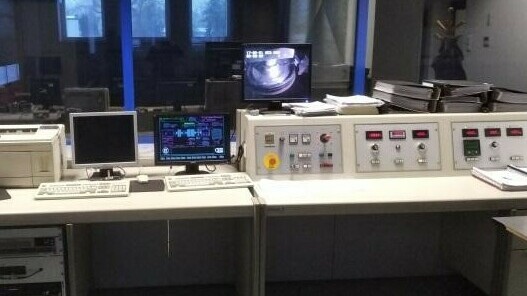
A perfect task for RDDS
The Instytut Kolejnictwa has defined four electrical systems for the modernisation of the test rig, which are essential for its intended use.
However, with the RDDS automation system, RENK has a tool at its disposal that combines all four systems on one platform.
Based on over 60 years of experience in operating its own test rigs, RENK has developed an automation system that focusses on the safe and successful execution of the test task.
RDDS (RENK Dynamic Data System) is a very powerful test rig automation system that supports the entire test process, from the preparation of the test to the actual execution and final storage of the results. RDDS offers adequate solutions for the daily problems of the test bench operator:
- Flexible adjustment of the test task
- Automation and standardisation
- Digitalisation of the test processes
- Operator friendliness
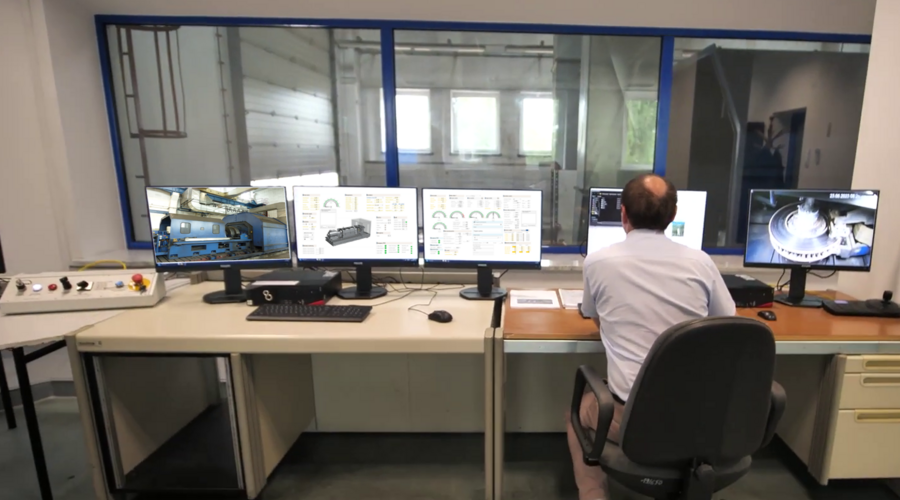
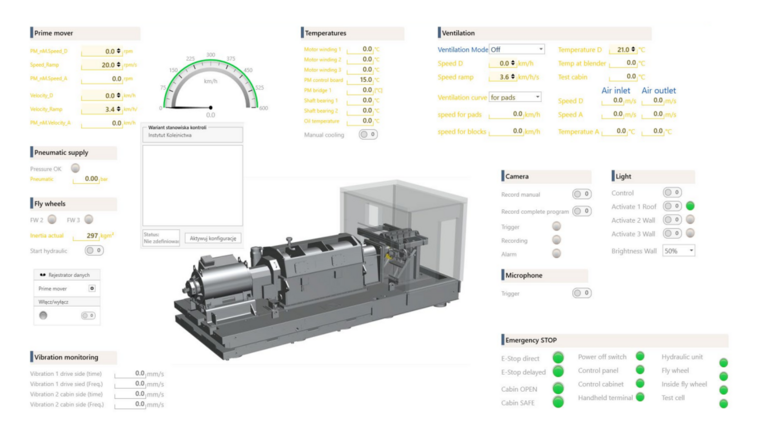
The control and monitoring system is responsible for monitoring the operation of all components on the test bench and the correct running of the correspondingly designed test programmes.
Using RDDS, these can be automated and monitored centrally. If a fault occurs in a component, the entire test rig reacts correctly and reliably. The complete digitalisation of the test process also enables automated processes in the interaction with the test rig. Automatic monitoring reduces the risk of operating errors and also enables autonomous operation of the test rig.
On the modernised flywheel brake dynamometer, the RDDS system mainly controls and monitors the following system components:
- Drive motor
- flywheel masses
- brake cylinder
- Air duct
- Wet test device
Today's development processes lead to increasing demands on the recording and processing of measurement data. With RDDS, all available results and information are recorded and stored in a database in a traceable manner.
The entire measurement technology of the test rig and test specimen is connected in RDDS via EtherCAT. Specially developed editors facilitate the calibration of the sensors.
All measured values can be displayed online and allow the test rig operator to evaluate the braking process at any time.
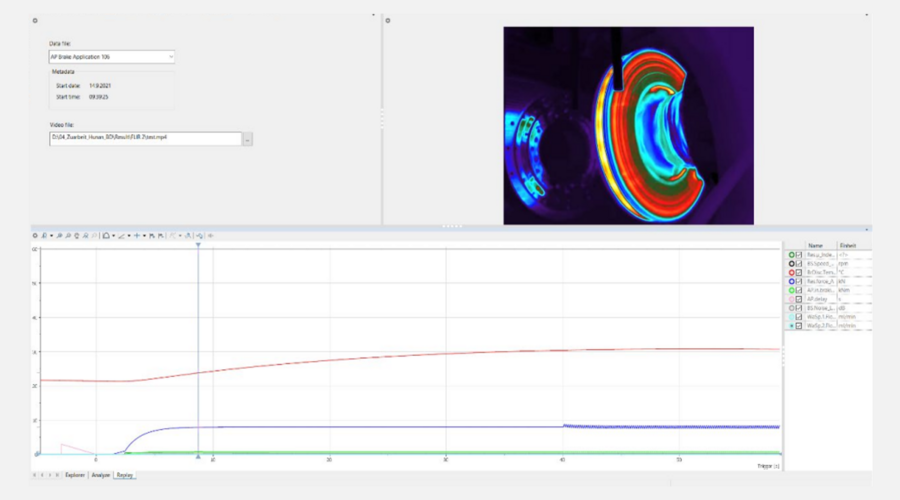
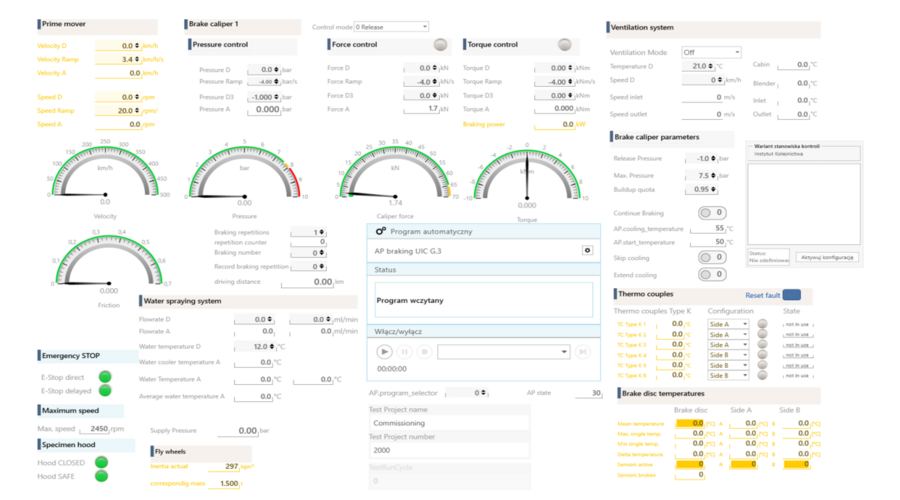
Using RDDS, the Rolling Stock Testing Laboratory now also has completely new options for designing test programmes.
The engineering of test runs can be carried out independently of the test rig in order to save valuable test rig time. The multi-client and multi-user functionalities available in RDDS enable the parameterisation of new brake tests in the database while the test rig is still busy processing another brake test. This preliminary work can be carried out at any designated workstations inside or outside the test rig. External engineering is an important component for maximising test rig availability.
Automatic programmes in RDDS offer a comprehensive option for creating automatic test sequences. The graphical editor makes it easy to convert manual tests into automated sequences and thus achieve reproducible results.
For optimum utilisation of the brake dynamometer, different test specimen types with associated test programmes can be stored in RDDS and loaded as required.
The complete digitalisation of the test rig and the test run enables RDDS to reliably monitor and diagnose all critical components and processes centrally. In the event of a fault in a subsystem, the entire test bench reacts correctly and the predefined safety routines are initiated automatically. The current system status is displayed to the test rig operator at all times. In the event of an emergency shutdown, RDDS uses the post-mortem recorder to automatically provide the previous and subsequent measured values at the time of the fault for fault analysis.
In combination with the monitoring safety controller, long-duration test runs with the flywheel mass brake dynamometer can now also be carried out autonomously and safely at night or on Sundays and public holidays (24/7)
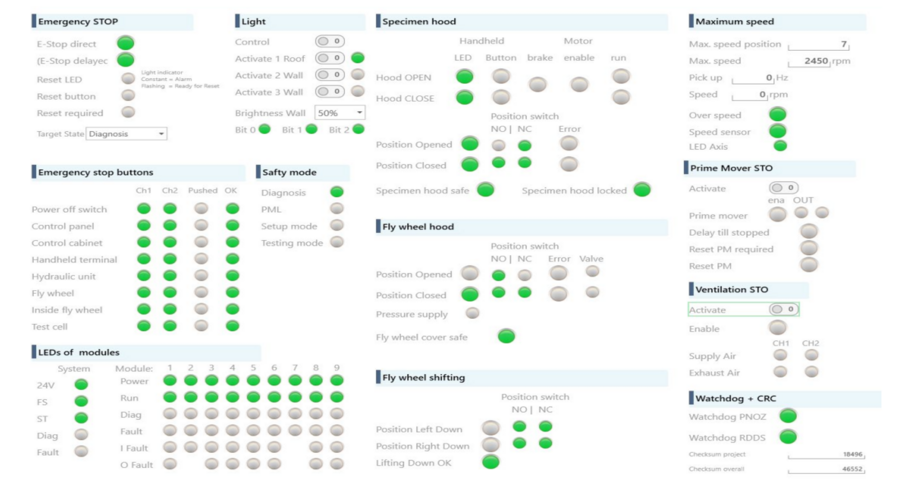
Familiar test rig, future-proof operation
The modernisation of the brake dynamometer at the Rolling Stock Testing Laboratory of the Instytut Kolejnictwa is a good example of successful test rig retrofits. Existing mechanical components provide a reliable substance when checked. New control, measurement and automation technology components are integrated in a targeted and effective manner. The result is a seamless fusion of proven substance and state-of-the-art technology and thus a technically and economically optimised solution for the future of the test rig.
For the Rolling Sock Testing Laboratory, the successful implementation of the test rig modernisation is of great importance, as it expands existing research capacities and enables research to be carried out more accurately, taking numerous scenarios into account. In this way, the test rig technology installed by RENK will contribute to improving the safety of railway transport in Poland.
Work carried out by RENK as part of the modernisation:
- Assessment of the test rig documentation of the initial manufacturer
- Inspection of the entire test rig
- Removal of electrical components
- Construction and installation of a new control and monitoring system
- Construction and installation of a new system for recording and processing measurement data from the tests
- Construction and installation of a new system for programming the test bench (designing of test programmes)
- Construction and installation of a new system for monitoring and diagnosing the test rig and components
- Construction and installation of a new wet test device
- Documentation of the modernisation measures carried out
- Acceptance of the entire test rig and handover to the operator
Need more information?
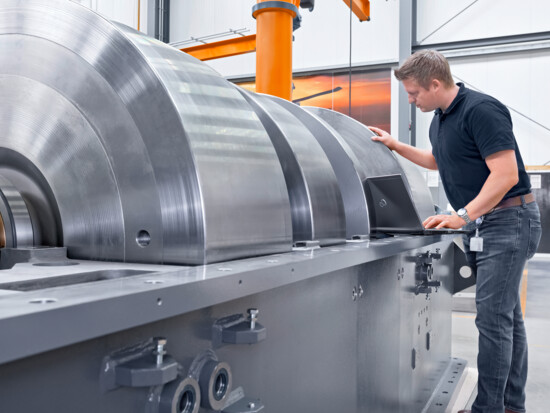
If you have any ideas or questions about our modernisation options, please contact our testing and project experts directly!