Nacelle test rigs
- 01Expandable multi-motor drive system
up to 35 MW - 025 DOF load application unit up to 113 MNm
- 03Testing of grid compliances
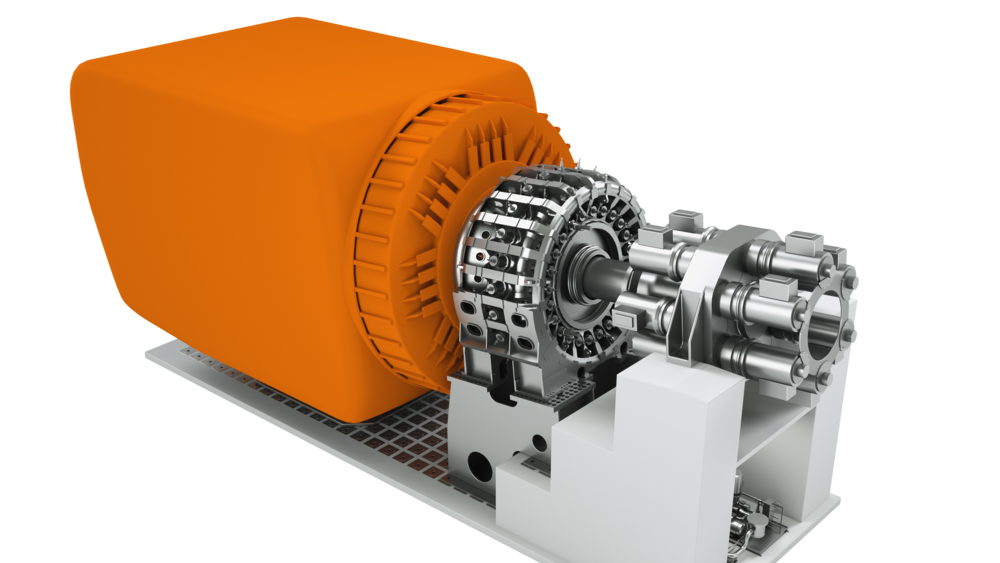
Our technologies for your demands
Nacelle test rigs from RENK are used for development support and quality assurance and basically consist of a drive system as well as an optional wind load application unit and a grid simulator.
A high availability as well as the exact application and verification of the required rotor loads are essential for the use of the test rig.
Our nacelle test stands are designed for the following tests, for example:
- Endurance and extreme load tests
- Conformance of production
- Prediction of life time/warranty
- Reliability prediction
- High accelerated lifetime tests (HALT)
- System performance tests
- Power curve and efficiency assessments
- Control system verification
- Design verification and validation
- Component validation and conformance testing
- Validation of physical and numerical models
- Grid code compliance and certification according to IEC 61400-21 and FGW TR3
Due to increasingly shorter development times for multi-megawatt turbines, we also pay particular attention to later upgrade options for our test stands.
Because of the turbine control system can also be linked to the RDDS automation system,
therefore RENK nacelle test rigs are prepared for full HIL and SIL functionality and one-man control.
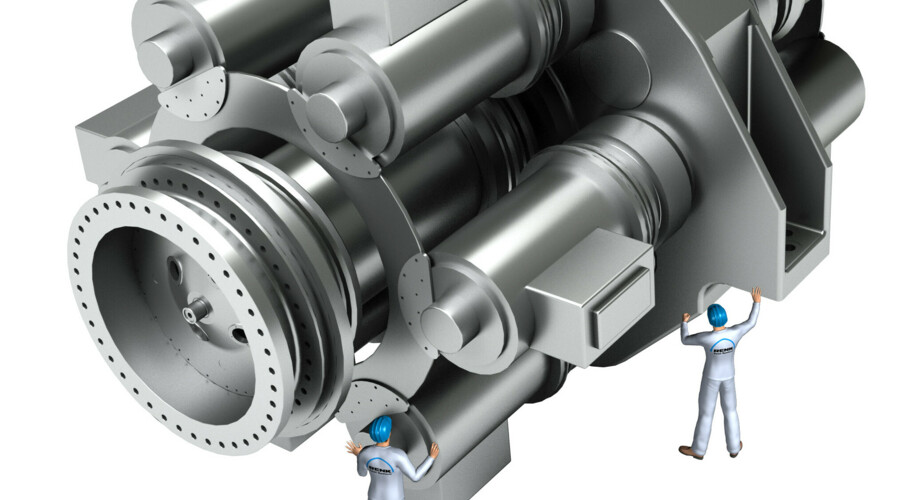
Expandable multi-motor drive system up to 35 MW
(43 MNm torque)
The main actuator on a nacelle test rig is the electric drive system, providing all static and dynamic rotary loads on the specimen drive train. This drive system has a very high torque and high dynamics in order to simulate all operating conditions occurring in the field. For this purpose, RENK has developed a multi-motor drive system whose performance (and thus costs) can be adjusted by the number of motors installed. In addition, the redundancy of the motors results in a highly reliable test system Test Systems Test systems assess technical components for function and durability. , which is particularly important for long-lasting fatigue tests.
Features and possibilities of RENK multi-motor drives
RENK has been successfully manufacturing multi-motor drives and generators for a variety of industrial applications for many years. At the DRIVETRAIN AND SYSTEM ENGINEERING CONFERENCE on March 21-22, 2023 in Aachen, Germany, our experts provided insight into the special features and possibilities of such a multi-motor drive.
Download the entire presentation on this event here:
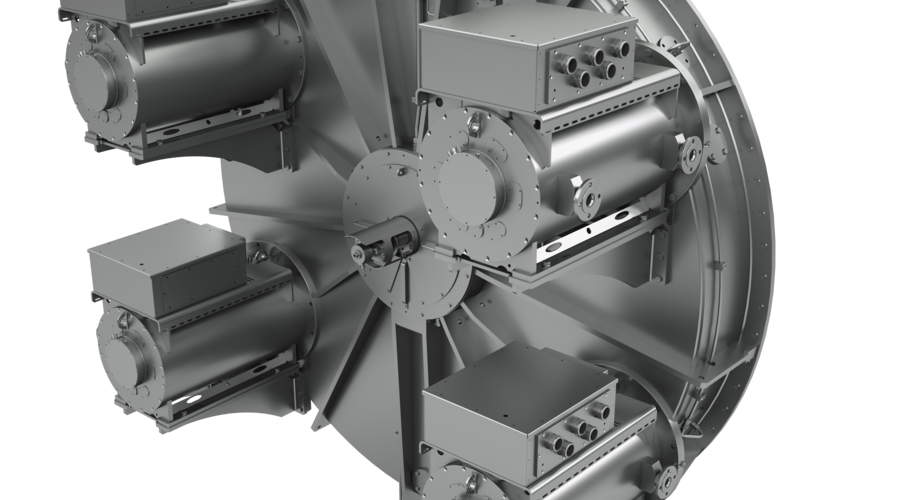
CWD / DSEC 2023: Multi-Motor Drive Technology in the Multi-Meganewtonmeter-Range
- RTS CWD 2023 (0.9 MB)
E-Mail angeben
Bitte geben Sie Ihre E-Mail-Adresse an, um den Download zu starten.
5 axis wind load unit up to 113 million Nm bending moment
In the rough operation of a wind turbine, constantly changing forces from all directions generate dynamic 5DOF loads on the turbine drive shaft. The total power of this stormy environment is given in test rig operation by the hydraulic load application unit (LAU),. To generate these forces and bending moments, RENK favors a hydrostatic disc for load transfer (D-LAU). This hydrostatic disc is directly connected to the main shaft of the turbine and is driven by the multi-motor drive system. Hydraulic actuators transmit the multi-axial loads to the rotating disk via plain bearing elements. This design only introduces minimal interference into the overall system and thus meets the highest demands in terms of measurement and control accuracy.
The plain bearing used has a calculated infinite service life and, unlike rolling bearings, never needs to be replaced - even under the highly demanding dynamic load collectives of a nacelle test rig.
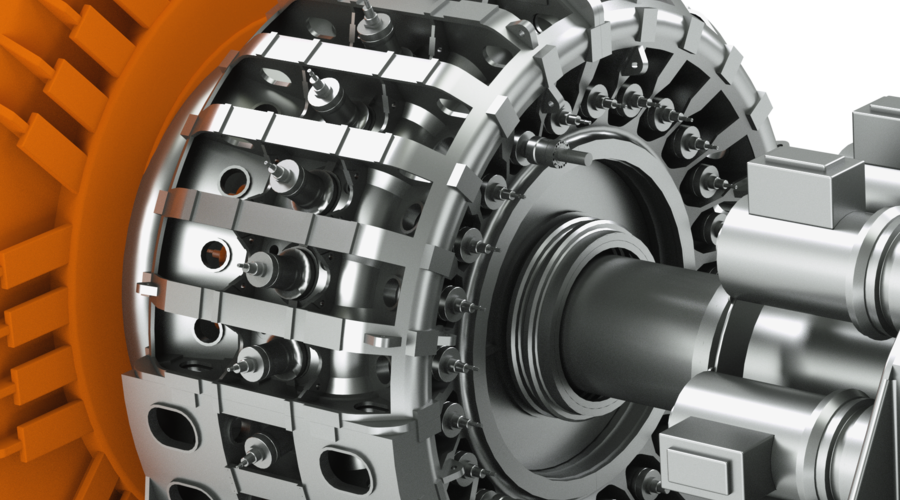
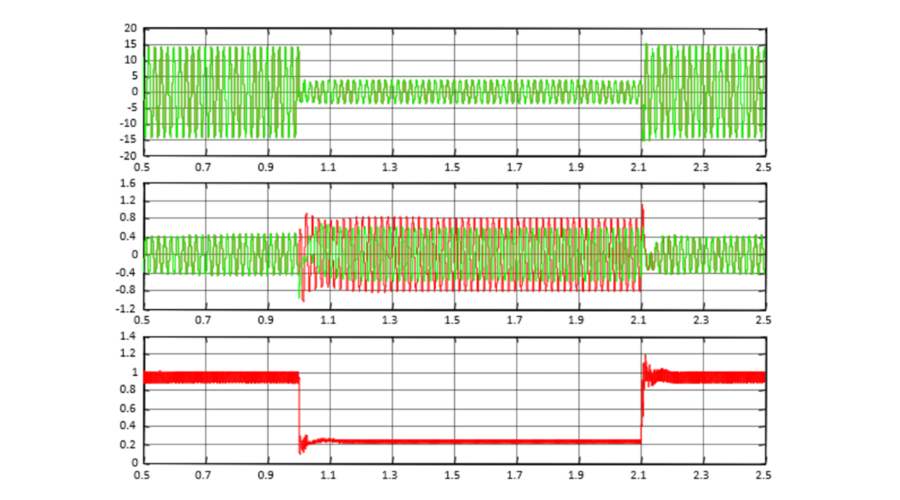
Scalable grid simulator for testing of grid compliances
The main electrical interface of the wind turbine is the interconnection to the public grid. For simple applications it is sufficient to feed the power, generated by the test object, back to the intermediate circuit of the test bench for recuperation. However, if this interconnection is also subject of the tests, a grid simulator can be integrated to simulate static and dynamic irregularities in the public grid (harmonics, LVRT, HVRT,...) in order to investigate their effects on the wind turbine behaviour.
Unique measuring and control accuracies
In dynamic operation, the measuring accuracy from the test specimen to the hydraulic actuators exhibits considerable losses due to the long distance. For this reason, RENK has developed a multi-channel measuring flange for very large loads; which is positioned directly at the interface to the main shaft of the test specimen. With this measuring flange, the applied loads can be recorded in real time without loss during rotation and taken into account in the test rig control. This multi-axial measuring flange, in conjunction with the virtually lossless hydrostatic loading device, enables unique measuring and control accuracies.
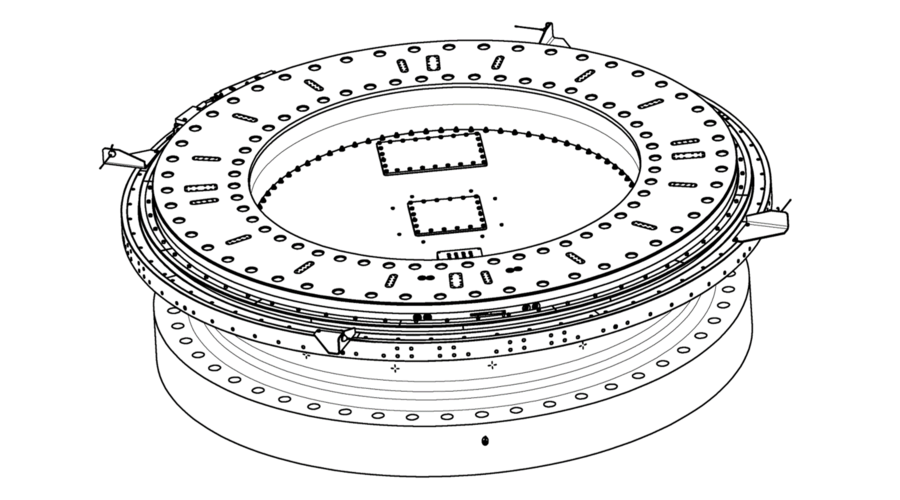
Features
- Testing of onshore and offshore turbines of all sizes currently in operation and under development
- Simulation of all loads on the drive train resulting from wind load (6 DOF)
- Multi-axis measuring flange
- Electrical closed loop for recuperation of generator power
- Extensive HIL/SIL capabilities
- Static and dynamic simulation of all fluctuations of the local power grid
- Unique measurement and control accuracies
- RENK RDDS test bench automation and data acquisition
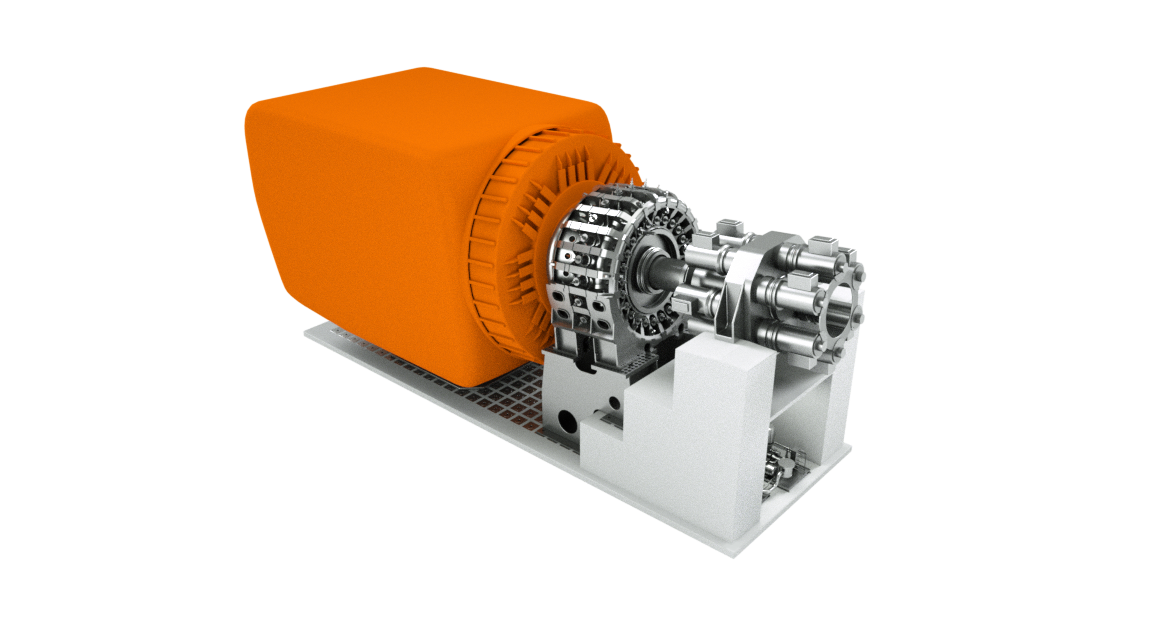
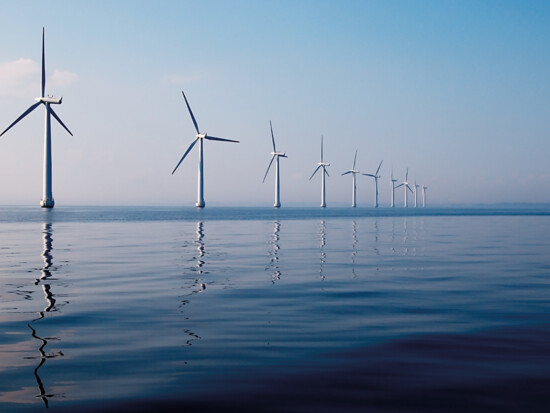
Get in contact with our experts from
Team Windpower: