Test rigs for main bearings
- 01Testing of complete mainshaft bearing assemblies or single main bearings
- 02Highly dynamic drive system
- 035 DOF Load application unit up to 113 million Nm
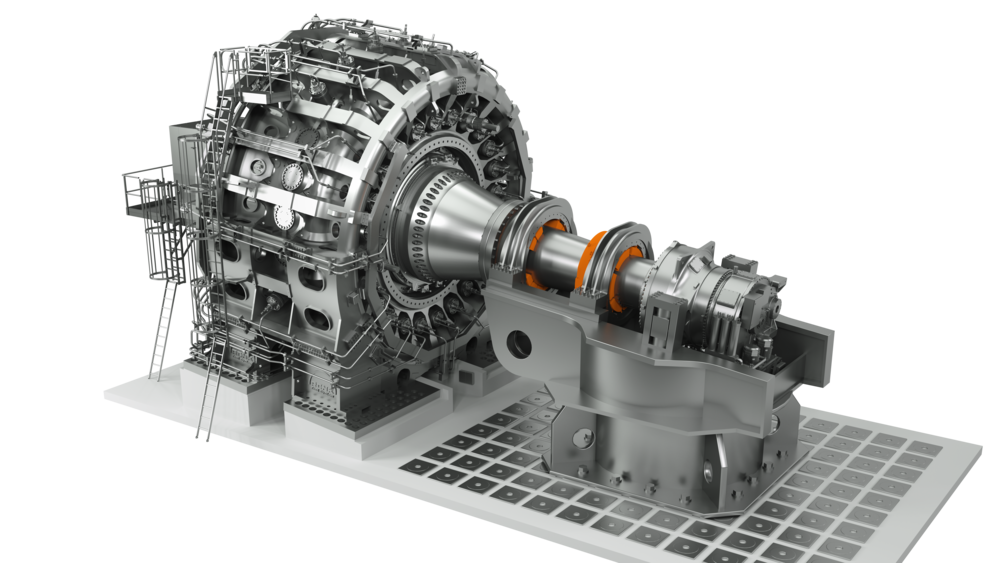
Our technologies for your demands
For testing bearings, larger support bearings with higher load ratings than the test bearing are also required. This is the only way to perform tests with overloads and to reliably assign measurement data to the test specimen. However, if the test specimen is the maximum in its class, e.g. main bearings of wind turbines, this requires special solutions.
For this reason, RENK has further developed its load application unit with hydrostatic disc (D-LAU) into a very sophisticated bearing test rig. With this design, not only very high loads can be generated quite precisely. Thanks to the multi-axis measuring flange mounted close to the test bearing, static and dynamic measurements can also be carried out reliably.
Regardless of which specimen type and specimen fitting is selected, our focus is always on the best possible test result without interference from the test stand. The integrated data measurement system enables the precise examination of all bearing components:
- bearing rings
- seals
- rolling elements and cages
- lubricating oil
In addition to the testing of rolling bearings, other bearing designs such as plain bearings can of course also be integrated as test items.
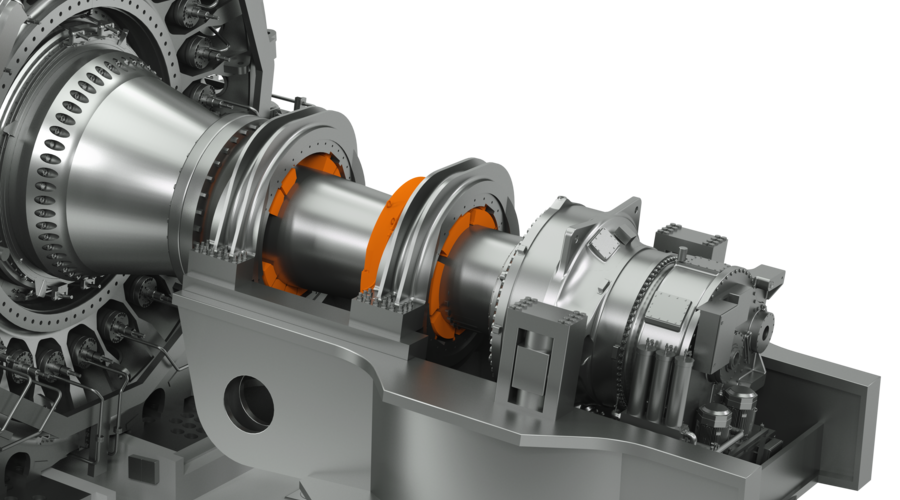
Different types of test specimens
In the front test stand area there is a large clamping plate on which a wide variety of main frames with main bearings or main bearing arrangements can be set up for testing. If the main frame of the wind turbine is not available, individual main bearings can be attached to the housing of the load application unit for testing using adapters. In this case, the loads applied to the inner ring of the test specimen are returned to the test rig via the outer ring and the adapter. Additional load support blocks in front of the load application unit are not required in this case.
Take a look at the load feedback on our bearing test rig when testing a single main bearing.
Highly dynamic drive system for standard and overspeed tests
The drive systems of RENK main bearing test rigs are designed to meet all necessary test requirements for today's main bearings and those in the planning stage. Starting from standard and extreme operating conditions onshore and offshore up to overloads or overspeeds in special tests.
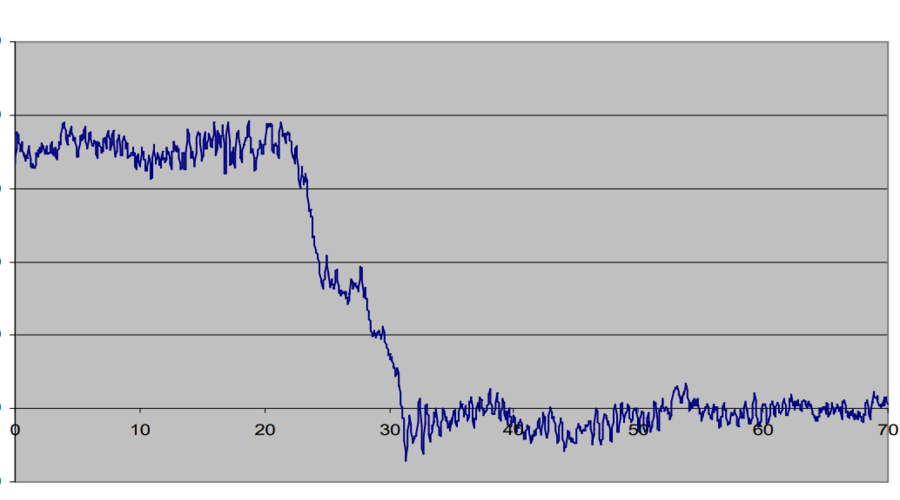
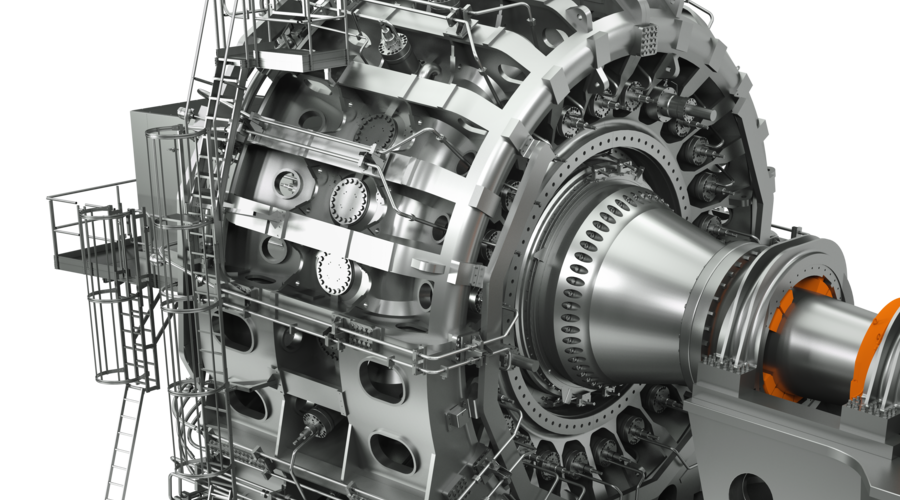
5 DOF Load application unit up to 113 million Nm bending moment
Decades of experience in the development of slide bearings Slide Bearings Slide bearings enable low-friction movement between fixed parts. at RENK led to this special form of load application. By changing the arrangement and number of hydraulic actuators, the load application can be easily adapted to the customer's needs. Very fine monitoring of the oil conditions in the sliding bearing elements results in a very functionally reliable overall system.
Minimal frictional torque in the load unit due to the use of hydrostatic bearings, even at low speeds and at standstill, make it possible to measure the frictional torque of the test specimen. These detailed measurements are not possible when using rolling bearings as test rig bearings due to much higher frictional torques.
Currently, such hydrostatic load application units are available in sizes from 8-113 million Nm bending moment.
Unique multi-axis measuring flange
As the world's only supplier of test rigs in the mega-Newtonmeter range, RENK optionally equips its load application systems with multi-axis measuring flanges mounted at the hub point of the nacelle main shaft. A linear transformation of the actuator forces to the hub point has proven to be not accurate enough due to the intervening distances in other test rigs. With this measuring flange, we can measure the actual applied forces directly at the test specimen, which is much more accurate, especially in dynamic operation.
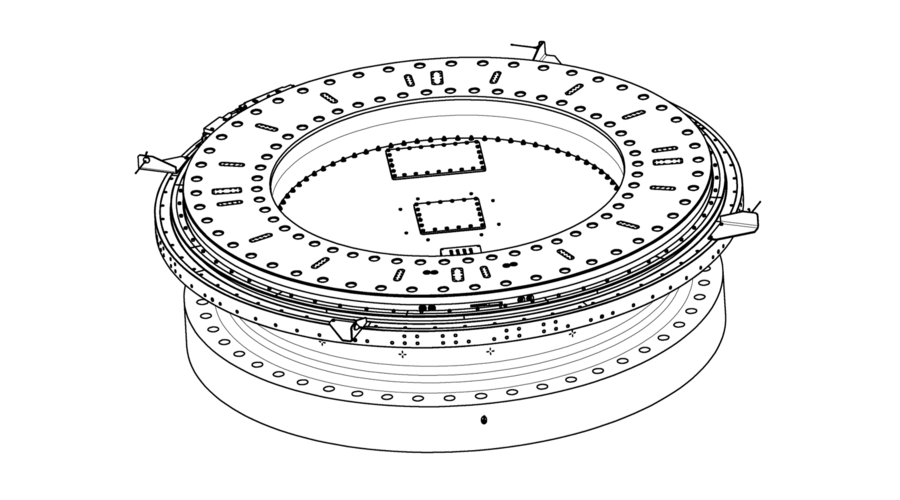
Features
- Testing of all main bearing designs of multi-megawatt onshore and offshore wind turbines
- Powerful and higly dynamic drive system
- 5 DOF load application unit based on pioneering slide bearing Slide Bearings Slide bearings enable low-friction movement between fixed parts. technology
- Multi-axis load measurement directly on the test specimen
- Shortest possible load circulation to reduce foundation loads
- Test piece preparation on external assembly station
- Unique measurement and control accuracies
- RENK RDDS test bench automation and data acquisition

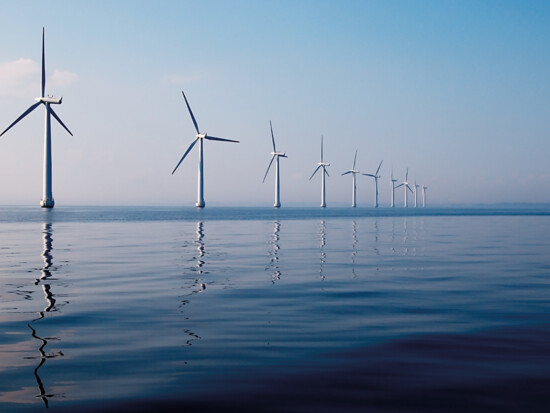
Get in contact with our experts from
Team Windpower: