RENK digital twins in test rig development and application
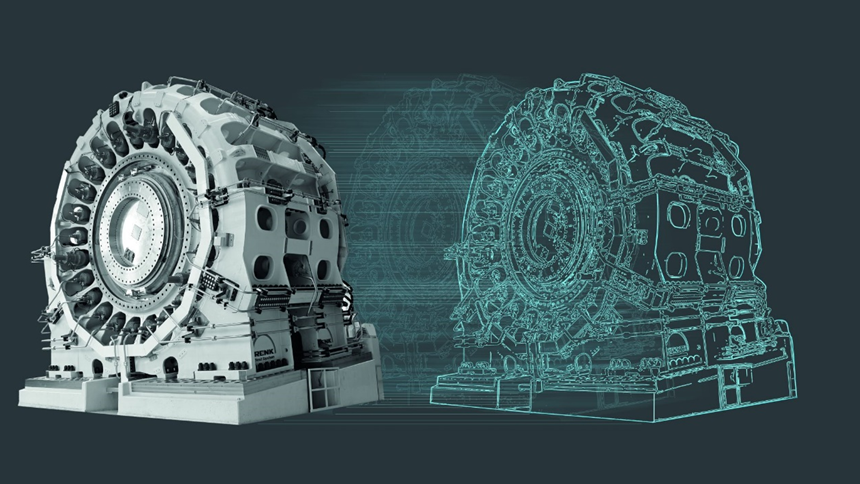
More than 15 years of experience in the design and application of digital twins
RENK is certainly one of the pioneers in the use of digital twins in test rig applications. In a specialised division, virtual models of test rigs and test specimens (DUT - devices under test) are prepared and simulations are carried out at component and system level.
The use of digital twins has long been standard in the aerospace industry. Based on joint project experience, RENK Test System Test Systems Test systems assess technical components for function and durability. GmbH (RTS) soon discovered this development tool for test rig development, where it offers immense added value for test rig manufacturers and customers.
The first commercial use of digital twins at RTS took place in 2010 with the development of two nacelle test rigs for Clemson University (USA) with test outputs of 7.5 and 15 MW. At that time, the focus of model based development was on the development and testing of controllers for hydraulic 5DOF wind simulation. We were able to continuously expand our libraries so that 10 years later, in 2020, we were able to model a helicopter main gearbox test rig for Leonardo Australia as a complete system for the first time and put it into virtual operation.
Today, digital twins are a standard tool in the development and operation of RENK test rigs. For our customers, the use of digital twins to set up an HIL environment is even mandatory according to the IEC 61400-21-4 standard for the development of wind turbines. Our test rig models can be used by our customers as a pre-simulation tool to generate xIL environments of the highest quality in accordance with valid standards or customer specifications.
The result is enhanced quality, reduced risks as well as time and cost savings.
Tools for test rig developers
In model-based design, digital twins form the centre of the development process and improve the way in which complex systems are successfully completed.
The big challenge in test rig development is the large number of different interacting actuators. To map this in model-based design, virtual replicas are created of all test rig modules. These subsystem models represent, for example, hydraulic systems, load units or drive systems with complete drive trains. By combining these subsystem models and considering interfaces and cross-influences, a comprehensive digital model of the overall system can ultimately be created. This model of the overall system not only supports the development of all control processes of the RDDS automation system, but also enables the optimisation of function-critical mechanical, hydraulic and electrical system components. This method therefore allows not only the development and testing of the controller, but also of the entire controlled system.
To this end, model-based design enables an efficient approach to creating a common communication framework for the entire design process in which a wide range of disciplines can check and optimise their interactions. By detailing the development process in subsystem modules and merging them step by step into the overall system, model-based design fully complies with modern V-model requirements in the development process.
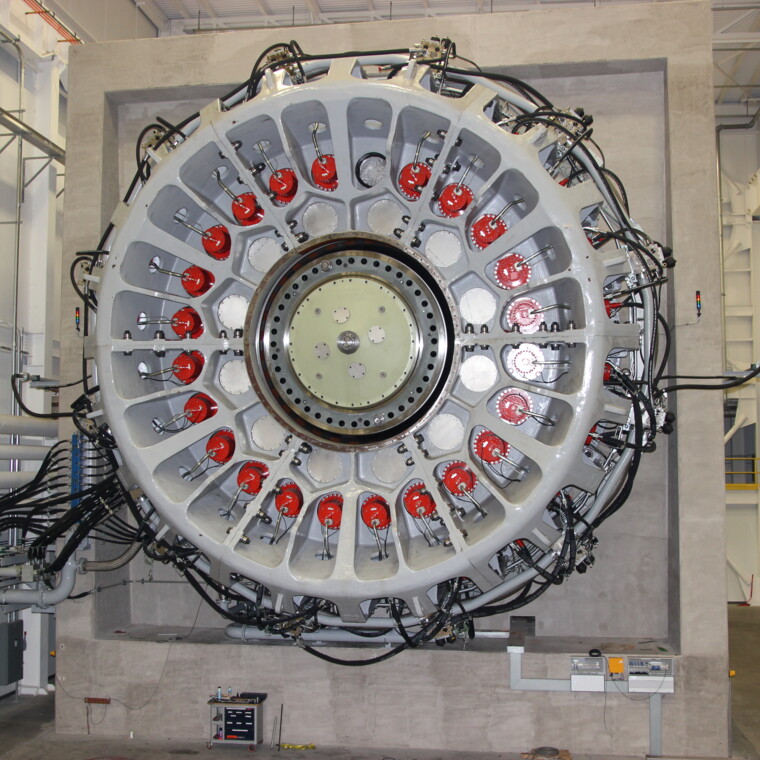
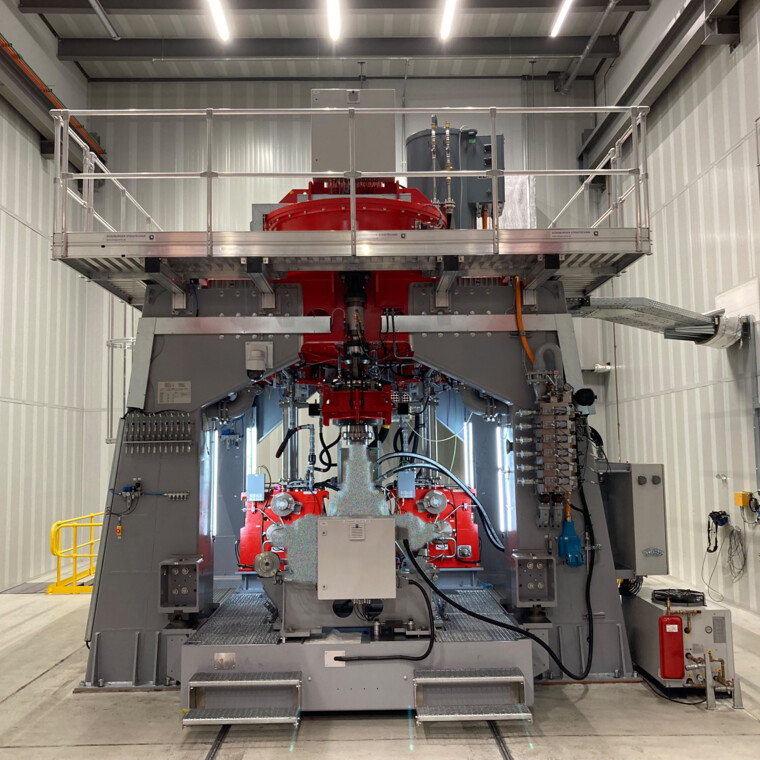
Once development is complete, the validated digital twins are then available for virtual commissioning.
Subsystems can be implemented and tested one after the other up to the complete system without the real system being present. During the defined simulation of errors, alarm values for error detection and shutdown routines for error reaction are defined. Later acceptance tests are also run in order to reduce risks during real commissioning. For the final real commissioning, only the digital twins have to be replaced by real test rig components and an extremely reduced commissioning with fully tested software has to be carried out.
A complex main gearbox test rig for our customer Leonardo Australia was the first digital twin of a complete complex test rig in 2020. Due to Covid19 and the resulting travel restrictions it was necessary to do the whole commissioning of the automation system virtually. The final real commissioning, which was reduced to a minimum as a result, and the training were carried out by individual people on site, who were guided by experts from Augsburg using augmented reality (AR) and virtual reality (VR) tools.
Virtual commissioning is now also used consistently at RTS for all complex systems. The significant reduction in commissioning times on site combined with more intensive quality control is proving to be an advantage for test rig manufacturers and customers alike.
Tools for test rig operators
A digital twin of the test rig including DUT as a pre-simulation tool also offers the test rig user considerable added value across all technical sectors. In combination with the real physical test system Test Systems Test systems assess technical components for function and durability. , the virtual system provides an almost endless xIL functionality for the development of software (SIL) and hardware (HIL).
DUT development and test run preparation
With the help of a test rig model available in the software, test runs can be carried out virtually, without hardware. This allows the user to check inputs and outputs before a real test run. Missing components can be replaced by virtual models.
This procedure saves costs by ensuring that the configuration is correctly prepared before real test time is used. It also reduces the risk of overloading the DUT by checking set points and alarm limits. Calculation algorithms used in the development process can be verified and further developed if necessary.
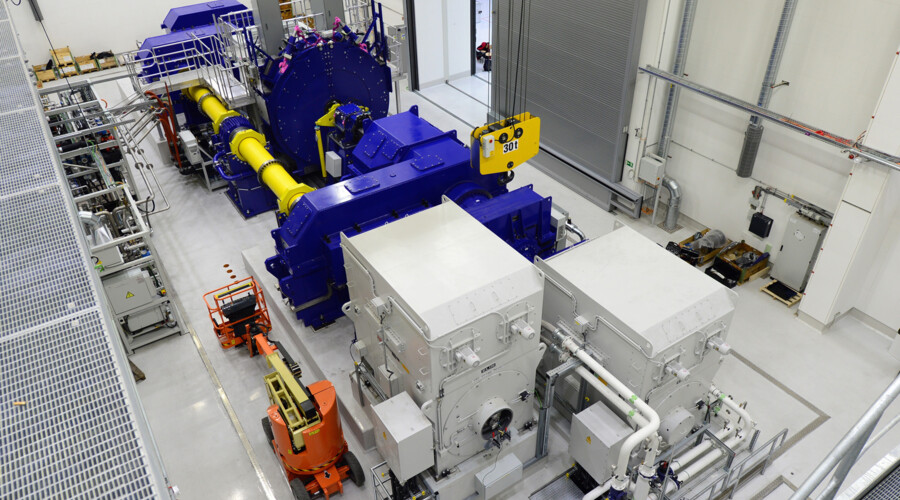
Test run performance
A digital twin can be linked to the physical test rig in real time. This allows sensor data and other relevant information to be continuously fed into the digital model. This real-time data integration makes it possible to precisely monitor system behaviour and make adjustments while the test is still running.
Digital twins can be used to perform dangerous or extremely expensive tests virtually. This minimises the risk to the test environment and the people involved and ensures that safety standards are met before real tests are carried out.
Monitoring the product life cycle
A digital twin can be used throughout the entire life cycle of a product or system, from development to production and maintenance. This enables continuous optimisation and adaptation of the system based on current data and findings.
Digital twins make it possible to recognise and predict potential sources of error at an early stage. By analysing the data from the digital twin, maintenance requirements and potential failures can be predicted, which increases the reliability of the system and reduces downtime.
Thanks to its many years of expertise, RENK is the preferred partner for integrating virtual models into real test rig operation - from model generation to application.
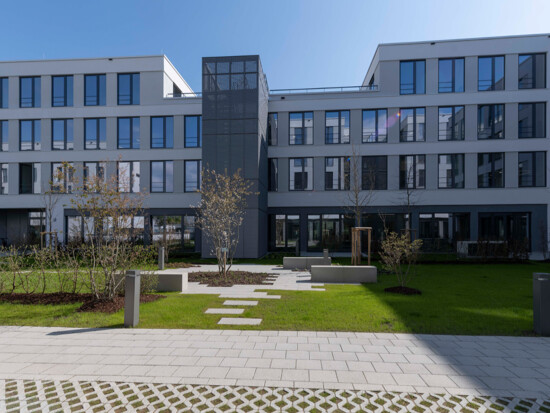
Contact us if you have any questions or would like to discuss your individual project.