Expansion of the Mercedes-Benz vehicle development test field by two NVH roller dynamometers
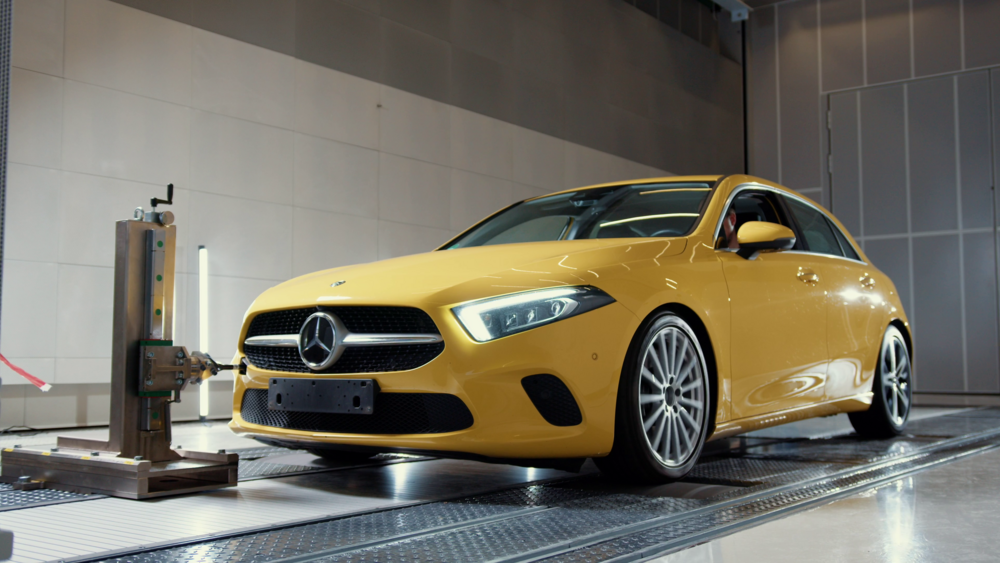
Trusted Partner
As a Trusted Partner for test rig technology, RENK gives its customers the space they need to concentrate fully on their core business.
Comfort in terms of noise and vibration is a core brand value of Mercedes-Benz. For the future safeguarding of the NVH (Noise, Vibration, Harshness) test field at the main development site, the renewal of two complete vehicle chassis dynamometers for acoustic development and powertrain integration was necessary. As a system partner, RENK has already installed several test rigs for this key customer.
Construction, and especially construction in existing buildings, means the extensive management of a large number of interfaces. As a total plant manufacturer, RENK takes on this task. Only intensive project coordination makes it possible to ensure overall system conformity with corresponding compliance with standards and guidelines for various trades. This results in a close meshing of subsystems such as room air technology, acoustically optimized blow duct, roller test rig, acoustic room lining, electrical charging equipment, fire protection and further technical building equipment.
The successful implementation is followed by a coherent service and support concept covering the entire lifecycle of the test rig. In this way, RENK supports its customers not only in the classic areas of maintenance and repair, but also in the common optimization of work processes on the test rig and in safeguarding the future use. An essential component is our open and graphically programmable control and automation system RDDS.
The brown field project at Mercedes-Benz in Sindelfingen
We speak of a brown-field project when an existing site is to be expanded or restructured, or has reached its capacity limits. In our case, Mercedes-Benz AG planned to replace two existing NVH chassis dynamometers at the Sindelfingen development center with new equipment featuring the latest technology. Because no major modifications could be made to the building, it was necessary to adapt the new test rig assemblies exactly to the existing basic conditions. This work had to be carried out during ongoing development operations in an existing building.
Scope of delivery:
For the realization of two new roller dynos, all system components had to be checked for further use and largely renewed. By bundling all trades at RENK, our customer was able to minimize the interfaces during the entire project and achieve savings in project duration and project costs. RENK ensures a coordinated meshing of different subsystems:
- Revision and partial renewal of the existing test rig foundations according to demand
- Complete replacement of the chassis dynamometers including all power electronics
- Development and integration of an optimized room acoustic lining
- Replacement of the exhaust gas extraction system and room ventilation system
- Implementation of an acoustically and fluidically optimized blow duct for vehicle cooling while retaining existing concrete duct runs in the building
- Integration of technical building equipment and essential system interfaces
- Implementation of a higher-level automation system based on RDDS
Our work extended in total from the floor to the roof, always under the premise of not interfering with the ongoing development operations in the neighboring rooms.
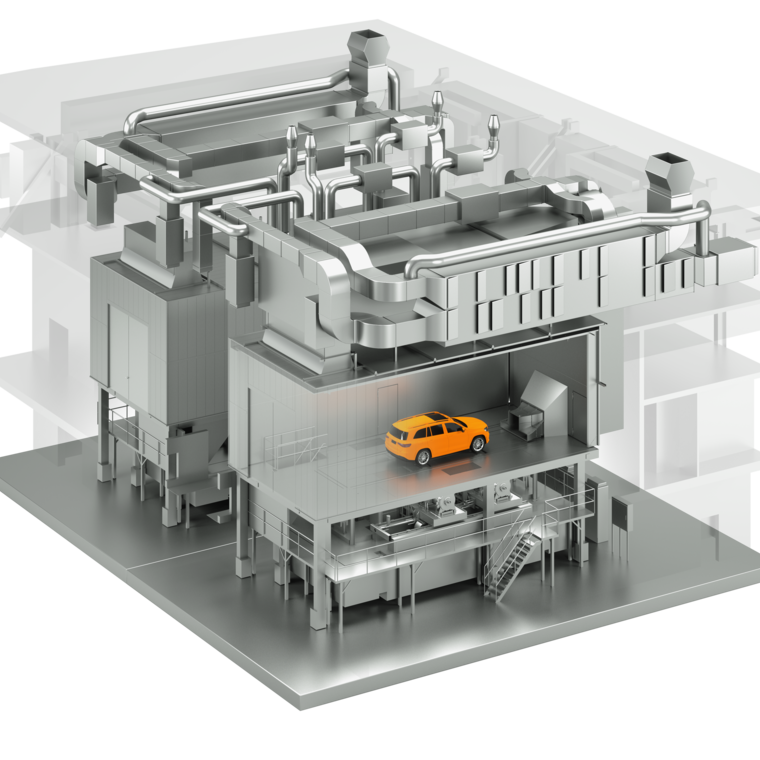
Innovative technical solutions
By performing detailed appraisals of the existing seismic masses, we were able to reuse parts of them, saving approximately 200 tons of concrete and several weeks of construction time.
The heart of our NVH chassis dynamometers is the roller set with roller diameters of approximately two meters (75 inches). The large rollers ensure that the rolling behavior of the tires of the vehicle is replicated as realistically as possible. For testing all-wheel drive vehicles, each roller is driven individually. Because development work is increasingly focusing on electrically driven vehicles, the test rig rollers must also be optimized for the characteristics of the electric drivetrain. The noise behavior also depends, among other things, on the precise torque distribution between the individual wheels. Direct, high-precision torque measurement enables precise control accuracy even under this increased measurement requirement. For this purpose, the roller sets including their drives must be designed to be particularly torsionally stiff. Torque calibration can also be performed under dynamic load conditions. The relevant technical solutions are absolutely unique and patented by RENK.
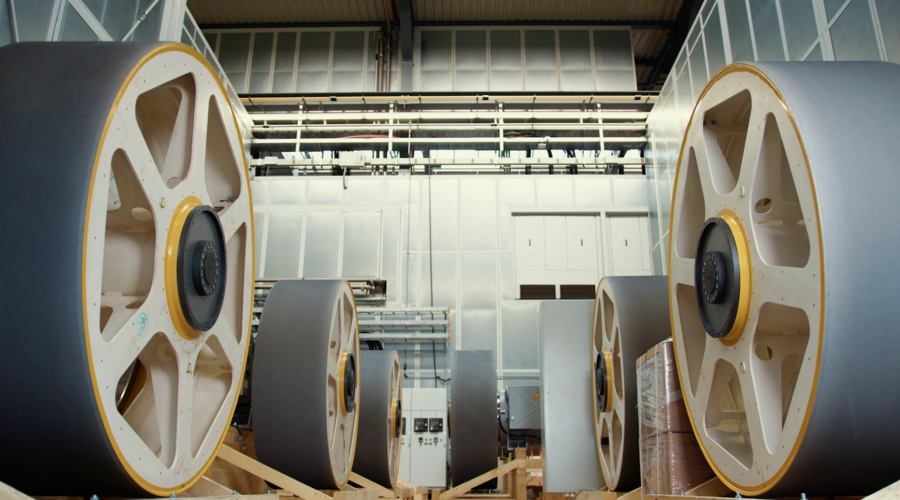
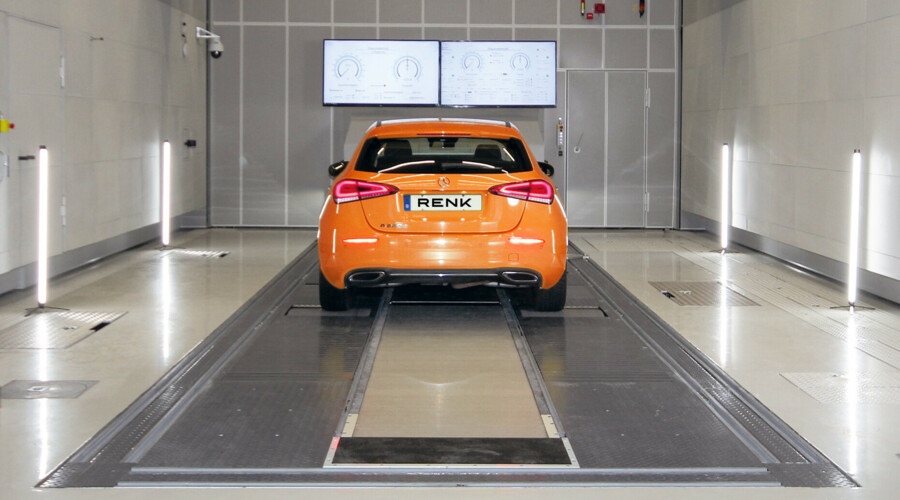
The sound absorbing lining of the test room is one of the decisive criteria for a successful measurement environment. New drive concepts increasingly cause high-frequency and tonal noise. Thus, there was a requirement to implement a room-acoustically optimized room lining in the existing building, which enables semi-frequency conditions over a large measurement radius, even with tonal excitation. The existing room dimensions were too small for the implementation of classic wedge absorbers. Therefore, RENK and its partner developed a new type of flat absorber with a partially asymmetrical structure. In this way, we were able to achieve an extremely high sound absorption of the entire test stand with significantly reduced space requirements.
New approaches were also taken with regard to the ventilation and air-conditioning system. Thanks to an extremely space-saving design and the partial reuse of existing structures, it was possible to largely avoid interfering with the building. Extensive flow calculations by RENK during the project planning phase were the essential key to the optimization.
A consistent heat recovery is also a permanent guarantee for a sustainable ventilation system that meets all the requirements of an NVH measuring room.
Pulse generator and data collector of both test rigs is our in-house automation system RDDS (RENK Dynamic Data System). Its intuitive handling and numerous graphical editors and library elements support the test rig operator in all development and operation tasks. At the same time, its open architecture also allows highly flexible adaptation to future measurement tasks. Equipped with additional mobile control devices, test runs can be carried out completely autonomously by just one person on both test stands if required.
For an optimized workflow, an extensive interface to the customer's NVH measurement system was also implemented in the RDDS.
Of course, the corresponding charging options for new drive types are also integrated into the overall system.
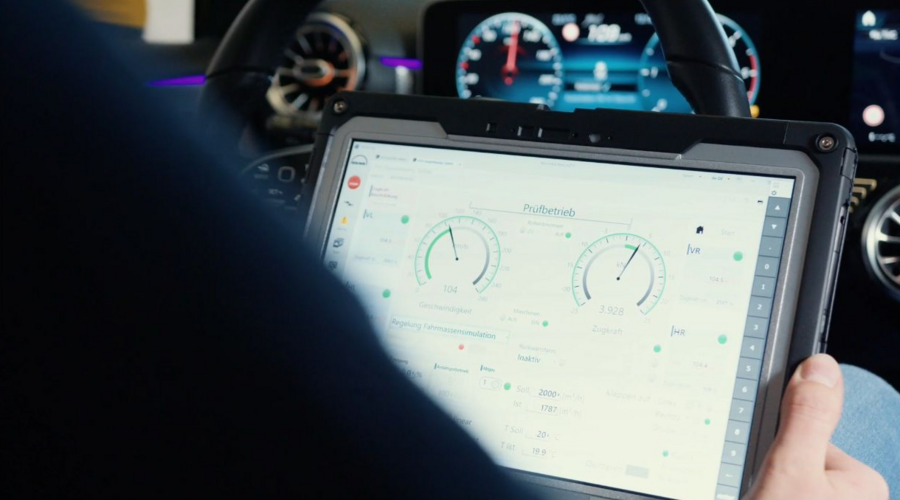
Full speed ahead with RENK at its side
The NVH experts of Mercedes-Benz now have two powerful and versatile test rigs at their disposal on traditional grounds in Sindelfingen, which are at the cutting edge of technology. The premium supplier is thus ideally equipped for new vehicle technologies and, in combination with the optimized workflows, will be able to process NVH measurement orders even more efficiently in the future.
Retrofits or complete rebuilds in existing facilities require maximum flexibility and a constant view of the overall project.
What can be reused?
How can today's technology be integrated into existing infrastructure?
What measures can be taken to minimize disruptions to ongoing operations?
With this project, RENK Test System Test Systems Test systems assess technical components for function and durability. GmbH has once again proven that it is not only a supplier of highly innovative test rig solutions, but also a system partner of the customer who can take on highly demanding projects holistically and reliably.
Key facts:
- Construction in existing building
- Turnkey project management
- Optimized room layout
- Realization one-person-operation
- Total traction force 40kN
- Rise time <10ms
- 350kW DC charging capability
- 0-100km/h airstream
- Room air conditioning 15-27°C
- 20dB(A) silence level
- 80 Hz lower cutoff frequency
- Integration MBBM PAK-live
Questions or you want to discuss your project ideas?
In case you have any ideas or questions in regards to testing equipments, from small to bigger installations, from green to brown field, from a single testing rig to a turnkey solution - involve our testing and project experts.
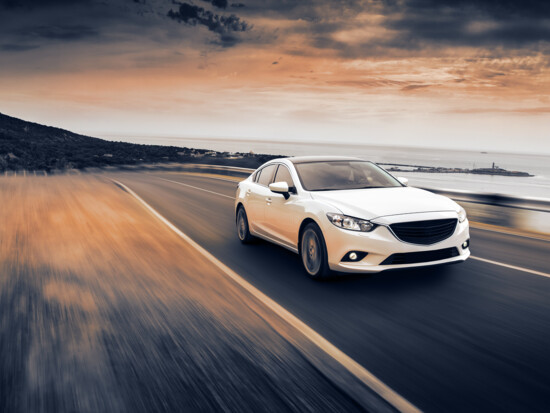
Get in touch in case you have any questions!