Wheel & Rail system test stands
- 01Optimized simulation of the endless rail
- 02Highly dynamic powerful drives
- 03Multi-axis hydraulic load unit
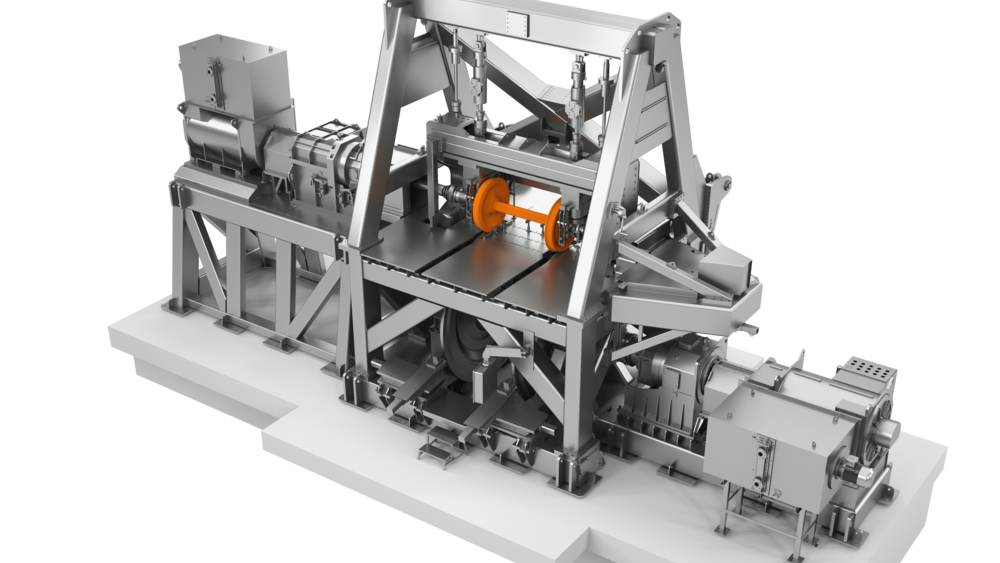
Our technologies for your demands
A perfect interaction between the wheel and the rail is required when heavy vehicles travel on tracks on a daily basis. RENK´s wheel & rail contact test systems Test Systems Test systems assess technical components for function and durability. reproduce this interaction perfectly in the lab setting.
A wheel-rail system test bench provides a wide range of testing options for all assemblies of the wheelset. All loads and environmental influences are realistically mapped, such as:
- Developing new materials and heat treatment methods for wheelsets
- Analyzing curve squeal and the influence of wheel absorbers
- Developing and calibrating diagnostic systems
- Analyzing lubricant distribution and damage pattern
- Optimizing wheelset axles
- Monitoring running dynamic behavior
The testing capabilities of a wheel & rail contact test rig are also very significant, especially in the development of braking systems:
- Examination of wheel slip under different environmental conditions
- Measurement of real friction values of wheel and rail under different environmental conditions
- Examination of the respective wheel-rail frictional contact
- Measurement of actual braking distances
In combination with these real-time measurements, a wide variety of brake control methods can be developed in the HIL environment of such a test rig to sustainably improve the braking behavior of future rail vehicles.
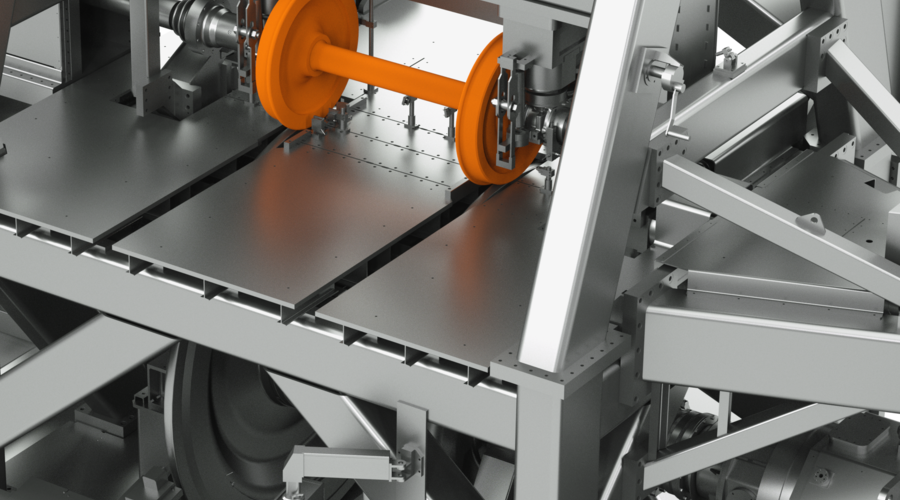
Rail to rig
To best simulate an endless pair of rails, we use two large rings simulation real rail track profiles. These rings are attached to the circumference of two large rotating disks and precisely aligned. In this way, we achieve trouble-free and realistic rolling conditions of the test wheel even at extremely high driving speeds.
Full power for various testing requirements
Test wheels and rail discs of the test stand are driven by separate highly dynamic and powerful drives. These drives not only enable the travel speeds of future high-speed trains, but also driving conditions such as acceleration or braking. Highly dynamic speed or torque changes are also possible, as required for the development of controlled braking systems.
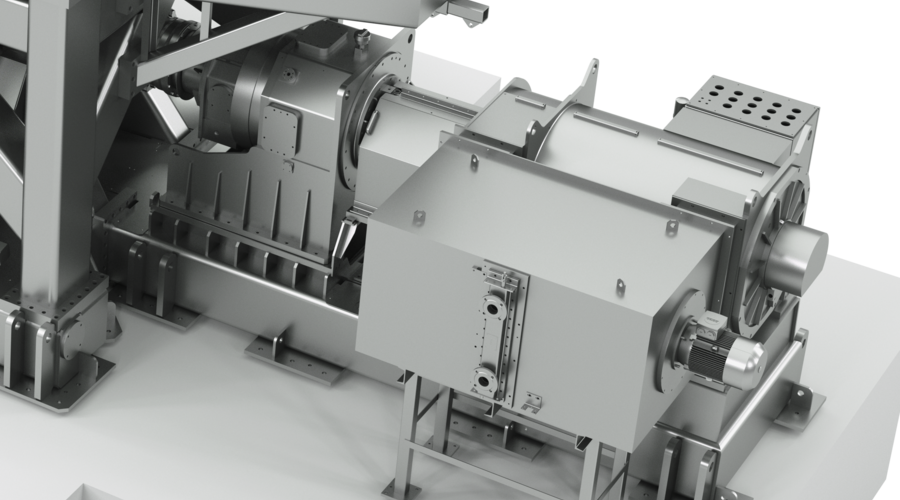
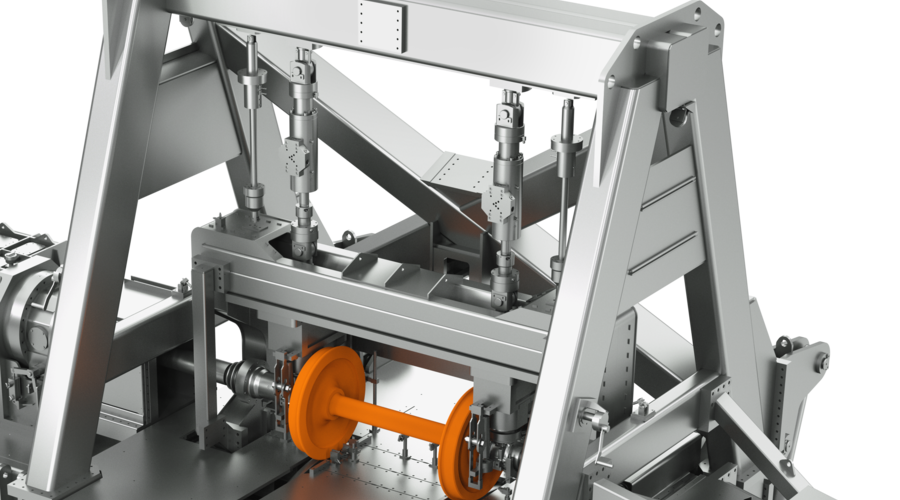
Simulating real loads
The available three-axis loading device is not only responsible for simulating the train weight on the wheels.
The highly dynamic control of the RDDS test bench automation system enables the simulation of vehicle weight and vehicle inertia in three dimensions under all static and dynamic driving conditions.
Features
- Test rig electronics with real-time capabilities
- Wear-free AC motor drive concept
- High-precision rail wheels for a realistic representation of continuous track
- Hydraulic load unit for controlled application of multi-axis dynamic loads
(wheel vertical force, thrust + lateral force) - Environmental simulation (rain, low temperatures, snow)
- RENK RDDS test bench automation and data acquisition
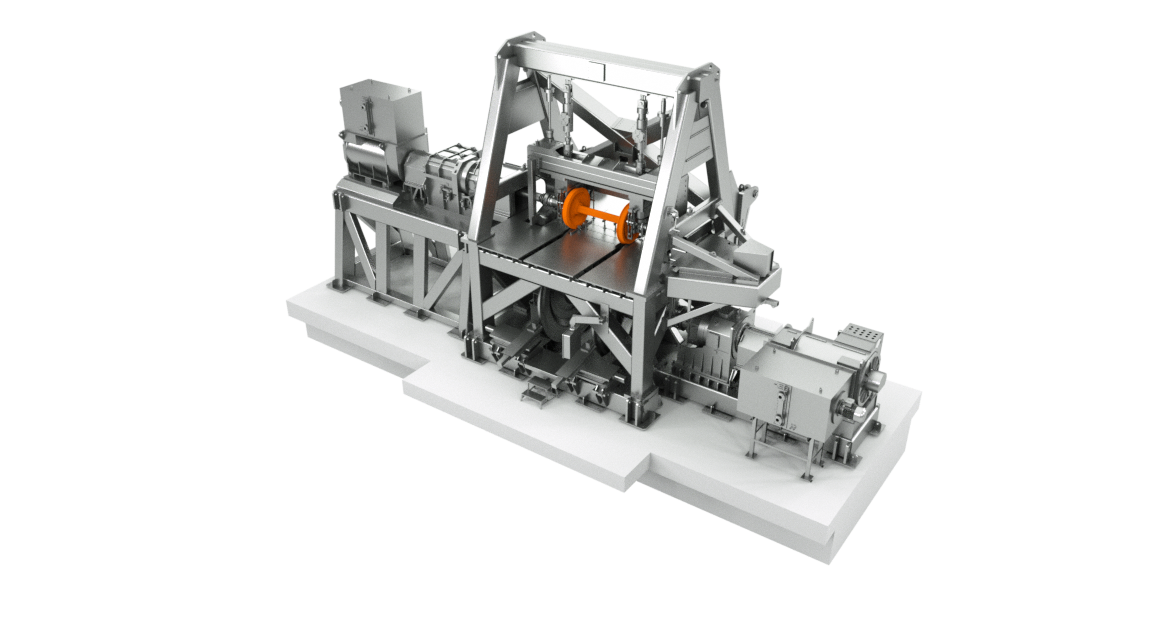
Take a look at Knorr-Bremse's development activities with the ATLAS wheel-rail contact test stand developed by RENK.
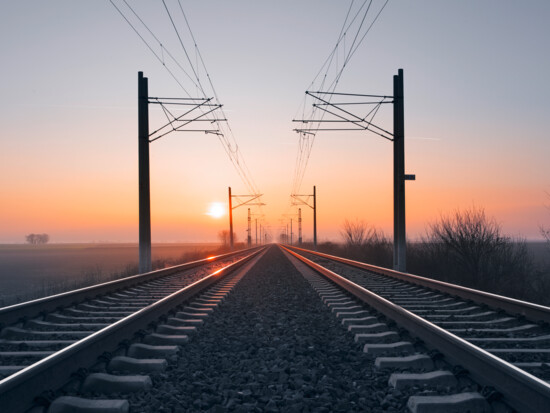
Get in contact with our experts from
Team Railway: