Development of a new type of overall vehicle test rig for motorcycles with the RENK automation system RDDS
Maximilian Stanglmayr, TUD Dresden University of Technology
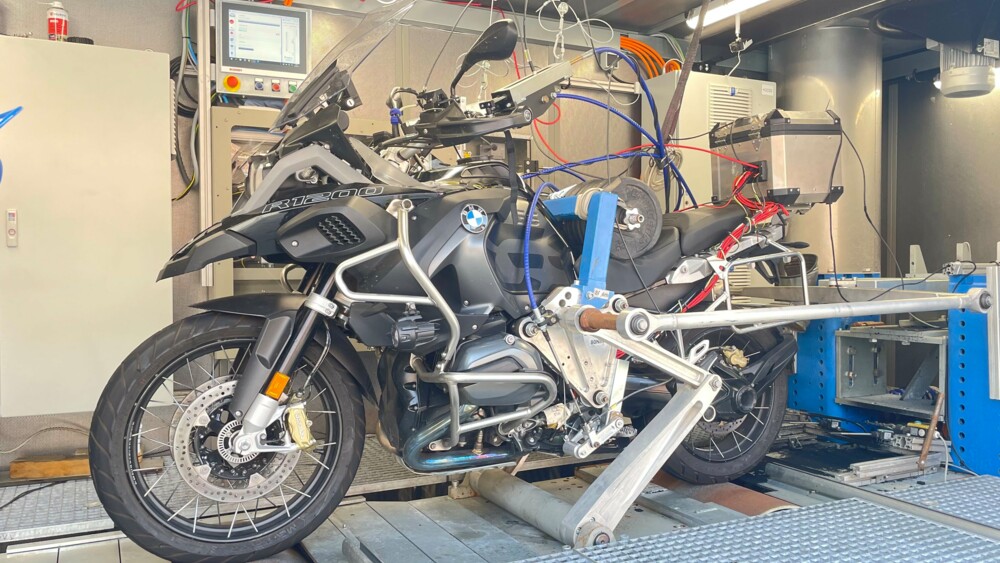
Next-generation motorcycle testing
At TU Dresden's Chair of Automobile Engineering, in close cooperation with BMW Motorrad, a new type of complete vehicle test stand for motorcycles has been developed that sets new standards in motorcycle testing. The system ensures high driving stability and includes the NVH characteristics (noise, vibration, harshness) that are essential for precise testing.
One innovative feature is the free-rolling front wheel, which allows the motorcycle to lift and tilt realistically. This significantly improves the accuracy of the test results. Thanks to the patented technology of the mounting system, the test rig replicates realistic forces within the motorcycle frame and ensures stable and repeatable measurements.
The motorcycle was controlled on the test rig using the RENK Dynamic Data System (RDDS). This project is an excellent example of the application of this software in scientific research, for which RENK offers special licence agreements.
The test rig was developed all the way from the prototype phase to industry-oriented implementation and is now available as a powerful tool for modern motorcycle development.
Real driving conditions transferred to the lab
My dissertation is dedicated to the development of an innovative motorcycle test rig that is designed to precisely replicate real driving conditions in a laboratory environment. The challenge is to accurately measure the complex vibrational and motional dynamics of motorcycles, as conventional test rigs are often only of limited use. The test rig should avoid dangerous or inefficient driving manoeuvres that would be necessary in real testing. By simulating real driving conditions, a safer and more efficient test environment is created that provides valuable insights without the risks and limitations of real-world driving tests.
The dissertation aims to provide a solid foundation for the development and validation of such test rigs and to support future developments in vehicle testing.
Special test rig features
Two very special features were developed for this test stand to fulfil the defined test tasks.
An outstanding innovation of the new test rig concept is the free-rolling front wheel, which is made possible by a patented holding system. This holding system clamps the vehicle in the centre of gravity, enabling a realistic reproduction of the longitudinal dynamic loads, including realistic pitching and lifting.
The system reduces contact stiffness and maintains the original vibration behaviour of the vehicle for precise measurement results. In addition, the holding system has a modular design, which allows flexible adaptation to different vehicle types.
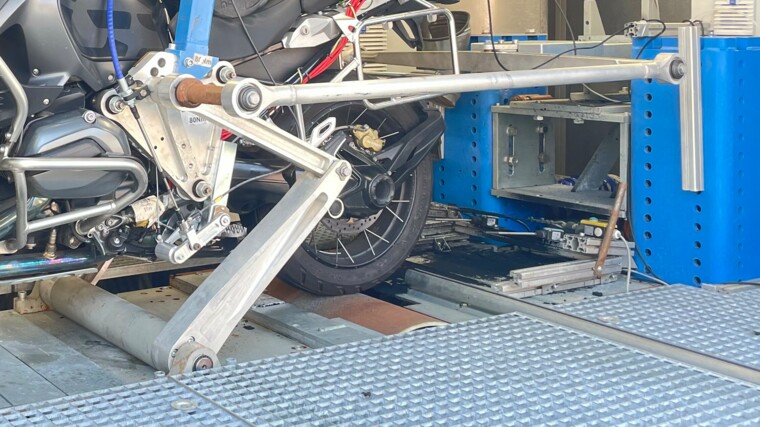
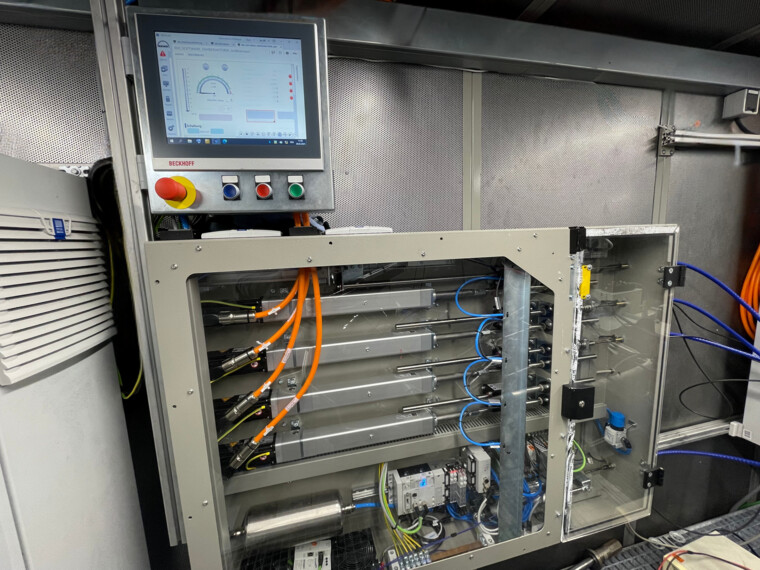
The test rig is equipped with an advanced driving robot system, which is automated by RENK RDDS.
This driving robot is equipped with five axes of motion, which are responsible for taking over the driving task of the motorcycle:
- Gearschift
- Clutch
- Throttle
- Breake rear wheel
- Breake front wheel
These operating elements are precisely actuated by means of RDDS-internal controllers at the original attachment points, such as hands and feet. Thanks to this multi-axis automated actuator, an exact and reproducible simulation of the driver interactions is made possible and the test accuracy is improved.
Realization of the test rig with RDDS
The development of the new motorcycle test stand began with the creation of a comprehensive concept that formed the basis for all subsequent steps. This concept was realised in hardware and rated a success by the project partners. The test rig prototype was then further developed in Dresden to further optimise its functions and performance.
A major advance was the integration of advanced driver actuators into the existing test system Test Systems Test systems assess technical components for function and durability. . We were looking for a modular system in which both software and hardware can be expanded as required and costs are manageable and transparent. RENK played a key role in this, in particular by sponsoring an academic licence for the RENK Dynamic Data System (RDDS). RDDS enabled the integration of readily available industrial electronics and provided the basis for precise control of the driving robot. The choice of Beckhoff TwinCAT as the real-time environment ensures reliable computing power and offers extensive expansion options via interfaces such as CAN bus and EtherCAT. An outstanding feature of RDDS is the ability to use Simulink models directly in the real-time environment, which allowed the control algorithms developed on digital twins to be efficiently transferred to the real system. For this test rig, an MBS model was created in VI-Motorcycle, which can be controlled by ADAMS/Controls in Simulink. This allowed the Simulink algorithms for switching and control to be tested and further developed at the desk before they were integrated into the real test rig control (TwinCAT / RDDS).
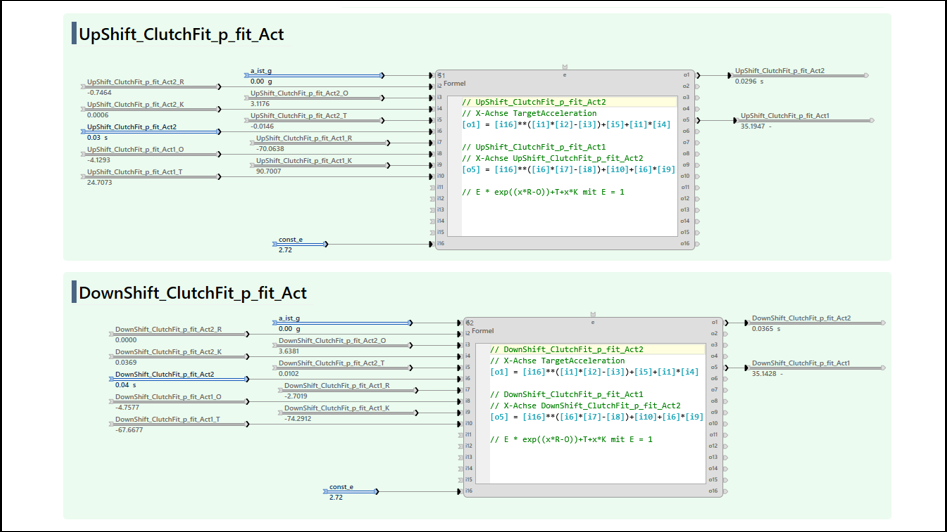
RDDS includes an integrated driver controller that makes it possible to calculate specific trajectories for gear changes based on various driving and load situations. To implement this feature, measurement data from different drivers were analysed and relevant parameters were identified and implemented in formulas for online calculation.
RDDS also offers outstanding possibilities to automate teach-in processes for actuators in new vehicles by means of user-friendly programming, which makes setting up new vehicles fast and efficient. The driver actuators are calibrated for vehicle-model-specific control paths.
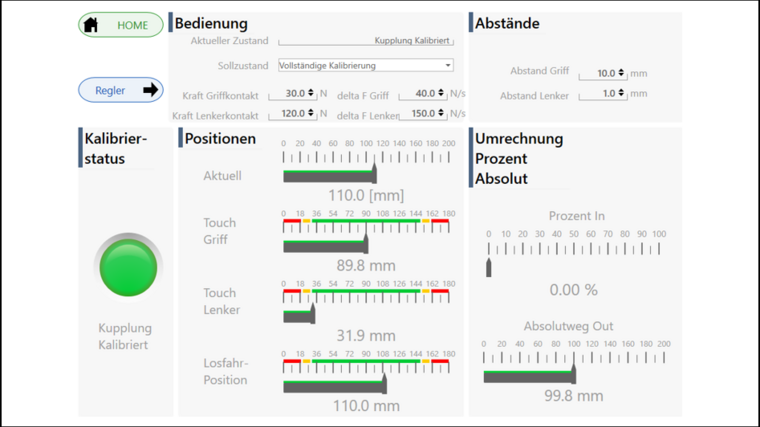
The data provided in RDDS are processed by the driver controller in real time and the calculated trajectories are continuously transmitted to the motion axes of the test rig. This ensures that the gear changes are simulated exactly and the test results accurately reflect real driving conditions.
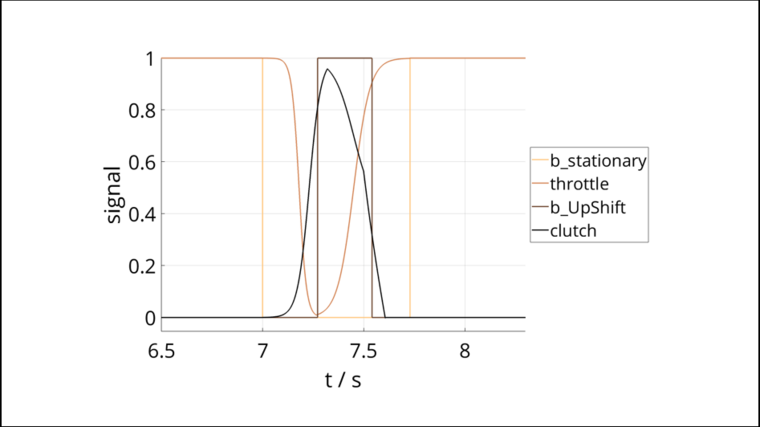
The shift model generated in this way makes it possible to follow a real speed profile with realistic shift commands. The speed profile, including the gear actually driven, is sampled over the distance and the shift parameters are determined as above according to the load situation.
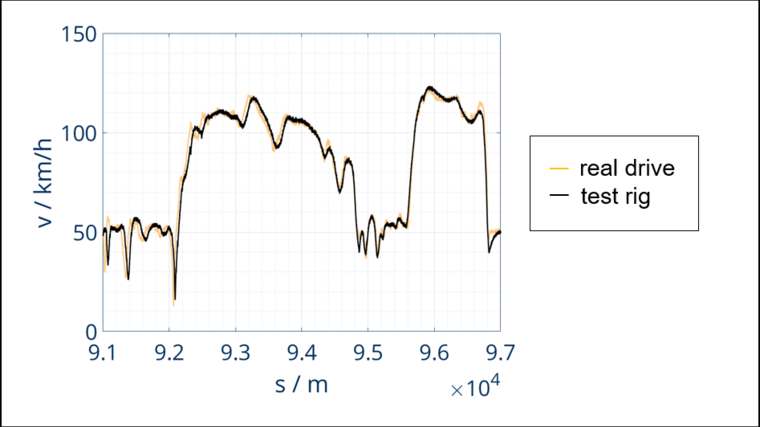
Goal achieved with RDDS
The newly developed motorcycle test rig enables precise reproduction of realistic driving conditions and sets new standards in vehicle testing. The main results show that the test rig generates realistic forces in the chassis, which match those measured when driving on the road. In addition, similar vibration modes were observed in both situations.
RDDS has proven to be crucial for the execution of extensive driving manoeuvres by considerably simplifying these processes. The integration of Beckhoff TwinCAT has enabled effective communication through standard interfaces such as CAN bus and EtherCAT. The test rig provides a solid foundation for further research and development in motorcycle technology and opens up new possibilities for precise vehicle testing.
Maximilian Stanglmayr
Maximilian Stanglmayr has extensive experience in the development and optimisation of test rig systems, especially in the field of motorcycle technology. During his time as a research assistant and project manager, he worked intensively on the design and implementation of complex test rig solutions. He was continuously active in the development of a complete motorcycle vehicle test rig, starting with the design phase and simulation and continuing through to realisation. In this context, he was responsible, among other things, for programming the automation software, integrating systems for measurement data acquisition and analysis, and realising and expanding the prototype test rig.
Of particular note is his role as the operator of the RENK Dynamic Data System (RDDS). Maximilian Stanglmayr successfully integrated RDDS to optimise the automation and adaptation of the test rig.
Do you have any questions or would you like to discuss your project ideas with us?
If you have any ideas or questions about the RDDS automation system for test rigs, please contact our test and project experts. We offer special licence agreements for universities.
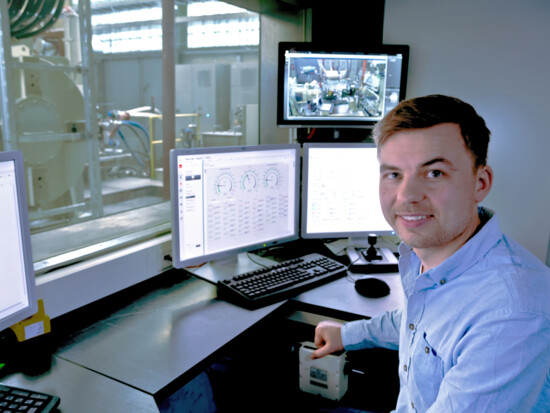
If you have any questions, please contact us!